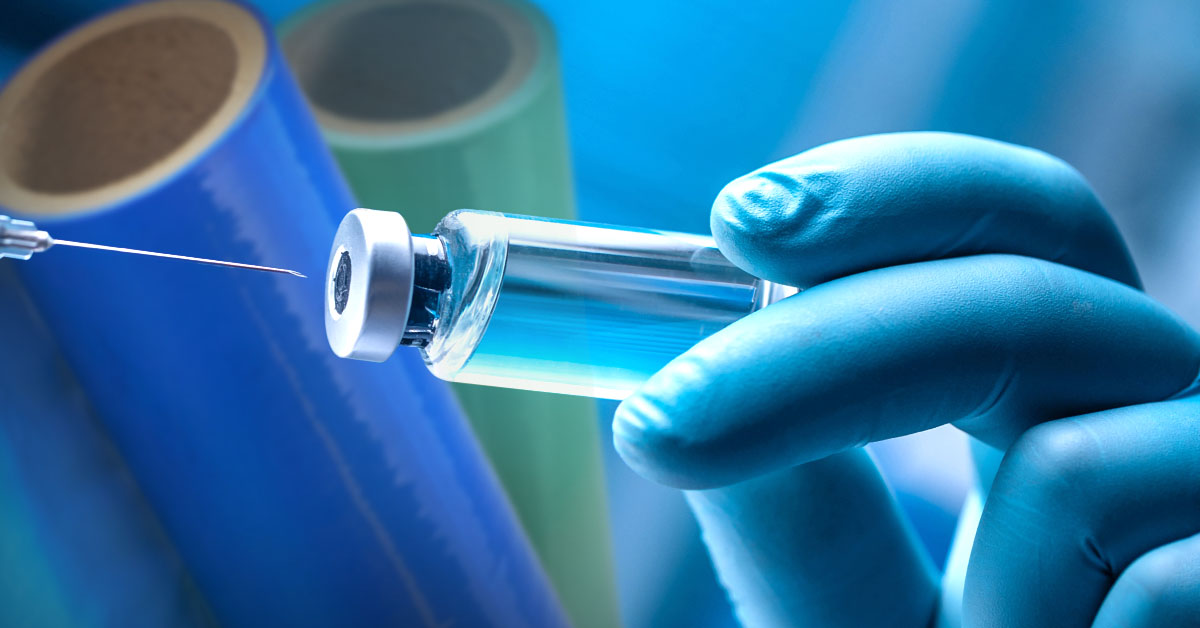
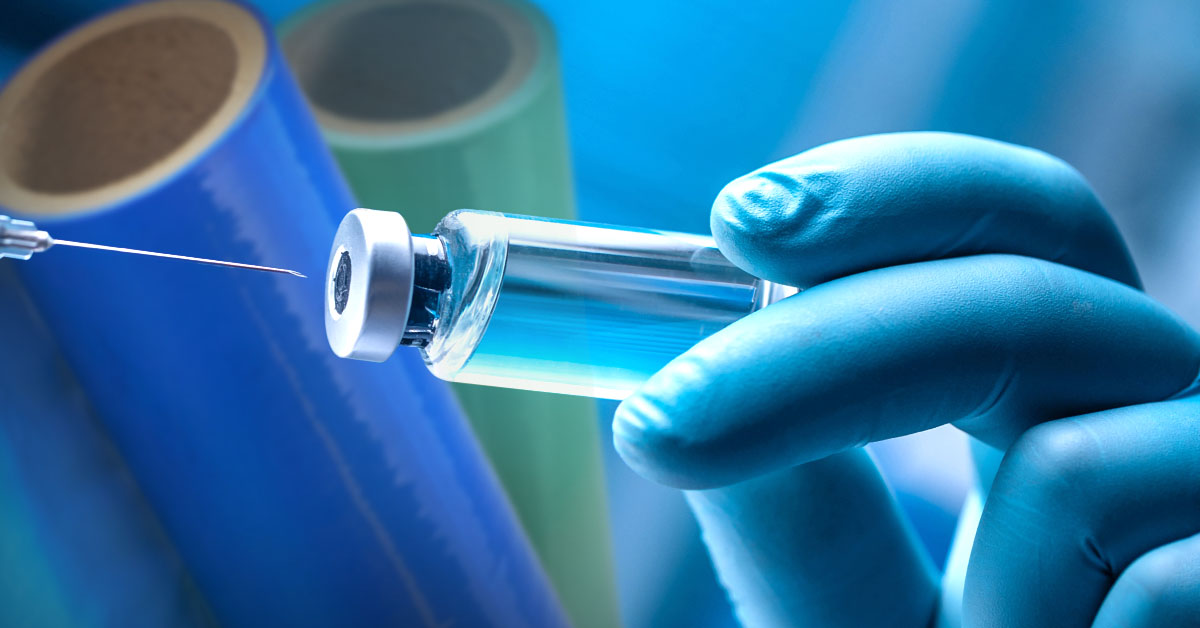
Chemically inert, bondable, pharma closures via engineered PTFE films
In an era where drug formulations grow increasingly complex and regulatory scrutiny intensifies, pharmaceutical manufacturers face mounting pressure to eliminate contamination risks while maintaining production efficiency.
Fluoropolymer films address these dual imperatives in pharma closure systems – the critical interface between drug products, environment and their containers.
The Hidden Engineering Challenge in Modern Drug Packaging
Pharmaceutical closures – whether elastomeric stoppers, plungers, or cap liners – perform a deceptively simple task: maintaining sterility and stability. However, the interaction between closures and drug formulations remains a persistent concern for formulation scientists and packaging engineers. Traditional rubber compounds can oxidise biologics, or adsorb sensitive APIs, potentially altering dosage efficacy.
This is where material science becomes pivotal. Versiv Composites DF1700 and DF3100 films employ a proprietary multilayer architecture that combines inertness with engineered bondability. Unlike some other Fluoropolymer layers that potentially delaminate under stress, these films form very strong bonds with butyl rubber and other elastomers through surface energy modifications. This structural integrity persists across temperatures from -200°C to +260°C – a critical advantage for closures subjected to lyophilisation or autoclaving.
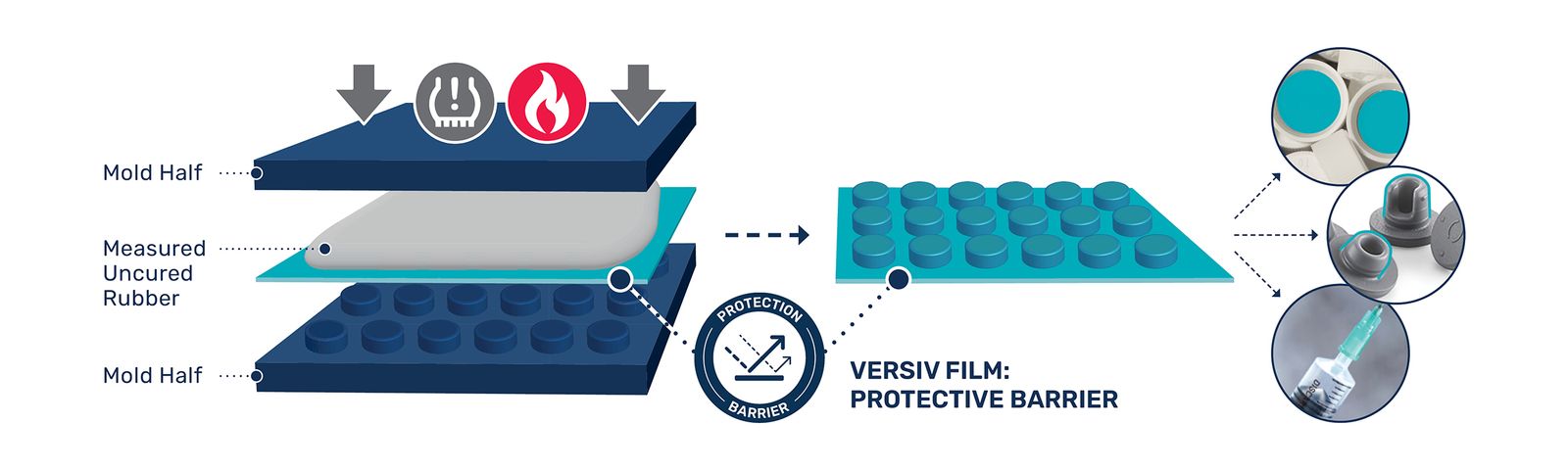
Pillars of Closure Performance
1. Barrier Engineering for Drug-Container Compatibility
The multilayer design creates graduated density zones within the film. Outer layers optimised for chemical inertness as well as wettability to prevent drug-closure interactions and allow for optimal bonding, while inner layers with tailored crystallinity enable elongation without additives to follow every contourof the required closure. Independent testing shows a high percentage reduction in extractables compared to standard laminated closures.
2. Manufacturing-Integrated Design
By co-engineering films with downstream processes, we have significantly reduced defect rates in production-scale trials. The films’ conformability also leads to a substantial reduction in trimming waste compared to less conformable PTFE foils.
Engineered Materials, Engineered Results
By reducing contamination risks and process variability, Versiv films help accelerate regulatory submissions while protecting brand equity. To explore how Versiv films can optimise your closure systems, contact our team for technical consultations or material samples.