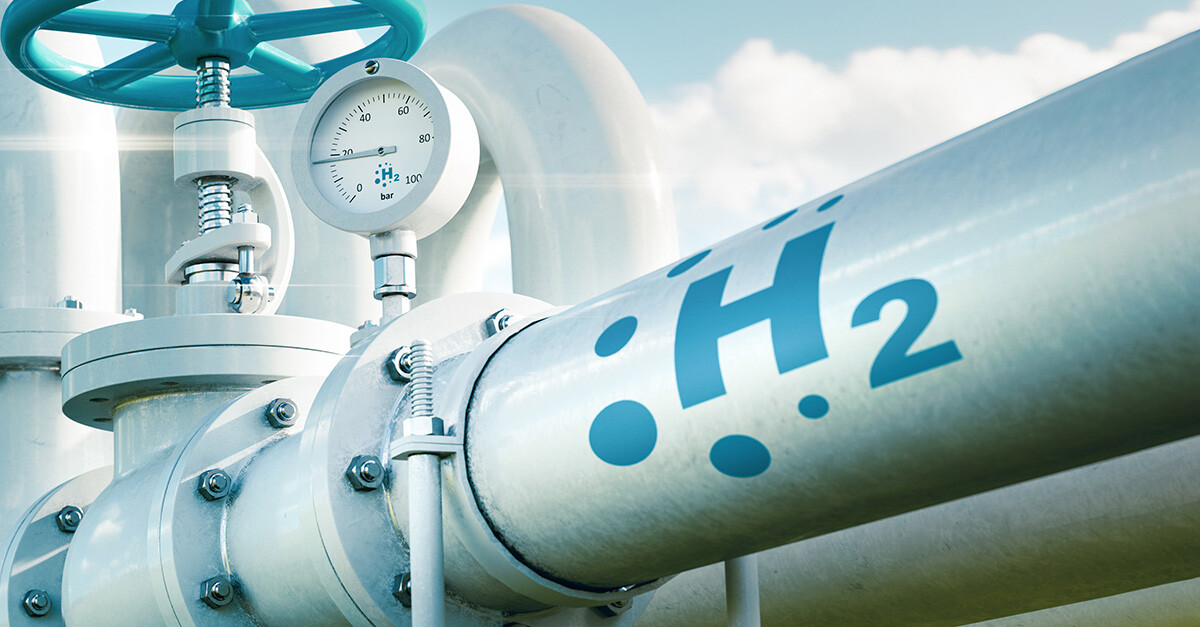
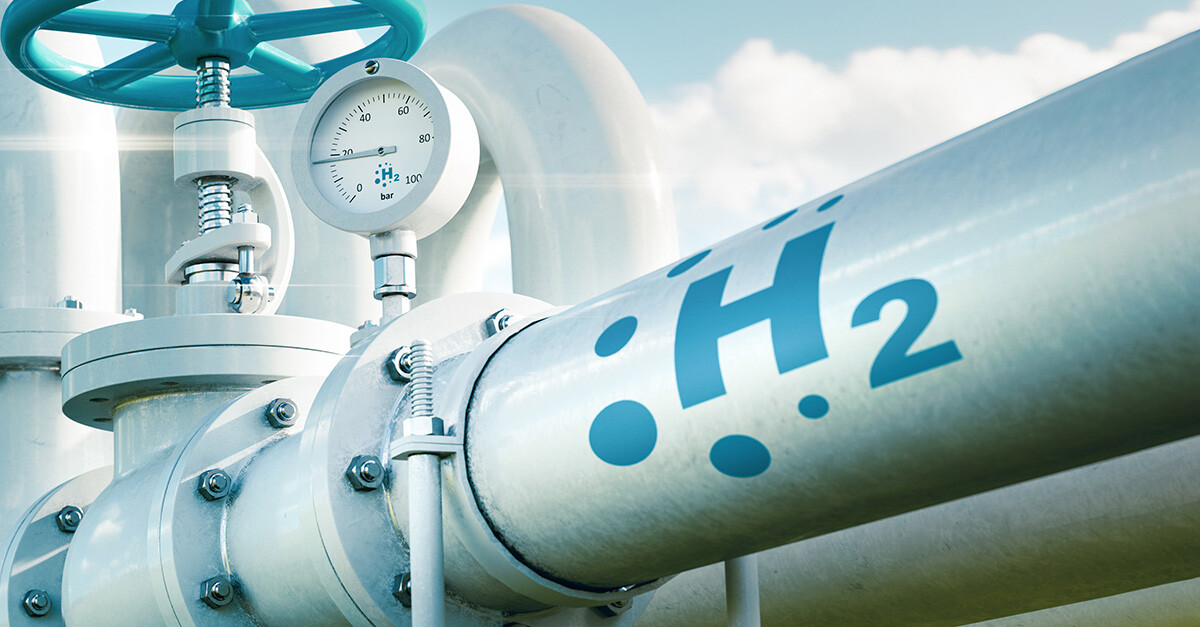
The steel industry is leveraging hydrogen generation technology for a greener future. Versiv Composites' fuel cells and electrolysers can play a role.
The mounting urgency to decarbonise and slash greenhouse gas emissions across all sectors underscores the pivotal role of green hydrogen in the energy transition.
Business certainty is a persistent anxiety among hydrogen industry stakeholders I meet at events, so the German steel industry’s recent move towards greening its operations is having positive ripples throughout the supply chain. Steelmaking requires a lot of energy, and that hydrogen is the chosen technology to deliver that energy is welcome. For those companies who contribute products aimed at maximising electrolyser performance, there will be a big demand to fulfil.
The steel industry has positioned itself as a critical player in the quest for a lower-carbon future. It represents a paradigm shift in how industries perceive their energy consumption and carbon footprint, especially for sectors like steel production that have been historically known for their significant contributions to global emissions.
Hydrogen—when produced through environmentally friendly methods—envisions a cleaner, greener future. Advancements in fuel cell and electrolyser technologies play a key role in this transition. Electrolysers, integral in splitting water into hydrogen and oxygen, and fuel cells, which convert chemical energy from hydrogen into electricity, are setting a new standard for energy efficiency and cost-effectiveness. The integration of such technologies is fundamental in crafting a sustainable manufacturing ecosystem—a vision that is increasingly becoming a reality.
The recent developments in Proton Exchange Membrane Fuel Cells (PEMFC), Alkaline Fuel Cells (AFC), Proton Exchange Membrane Electrolysers (PEMEL), and Alkaline Electrolysers (AEL), as documented on our recent white paper, are at the forefront of steering this journey towards a decarbonised world.
The climate policies being unrolled globally, coupled with technological breakthroughs in renewable energy sources like solar and wind, are making the large-scale production of green hydrogen more feasible and competitive than ever before. The European Union's Hydrogen Strategy aims for a significant installation of renewable hydrogen electrolysers by 2030, highlighting a concerted effort towards green hydrogen adoption. This not only elevates the market for PEMEL and AEL technologies but also fosters an environment ripe for research, innovation, and development.
As it is there are plentiful products already available to facilitate the new dawn of hydrogen. At Versiv Composites, we have a well-established stable of products to aid the decal transfer method in electrolysers and an array of gasket materials suited to electrolyser and fuel cell applications.
For example we provide quality catalytic layer production solutions for Catalyst Coated Membranes (CCMs) used in electrolysis. Versiv DF100 5 mil substrate achieves both requirements involved in the process: it has sufficient surface energy for wettability while also allowing for effective transfer. Other products in our range used as decal substrates include DF100 3mil, DF29NSP 67, CF103, and derivatives such as CF205, SRF103, and SRF205 — all of which serve as decal substrates. Versiv also serves materials suitable for fuel cell and electrolyser gaskets such as DF29219 and DF2929.
Stakeholders throughout the industry now await how this industrial plan unfolds, but at this juncture it looks a very positive step and goes some way to providing certainty to market operators.