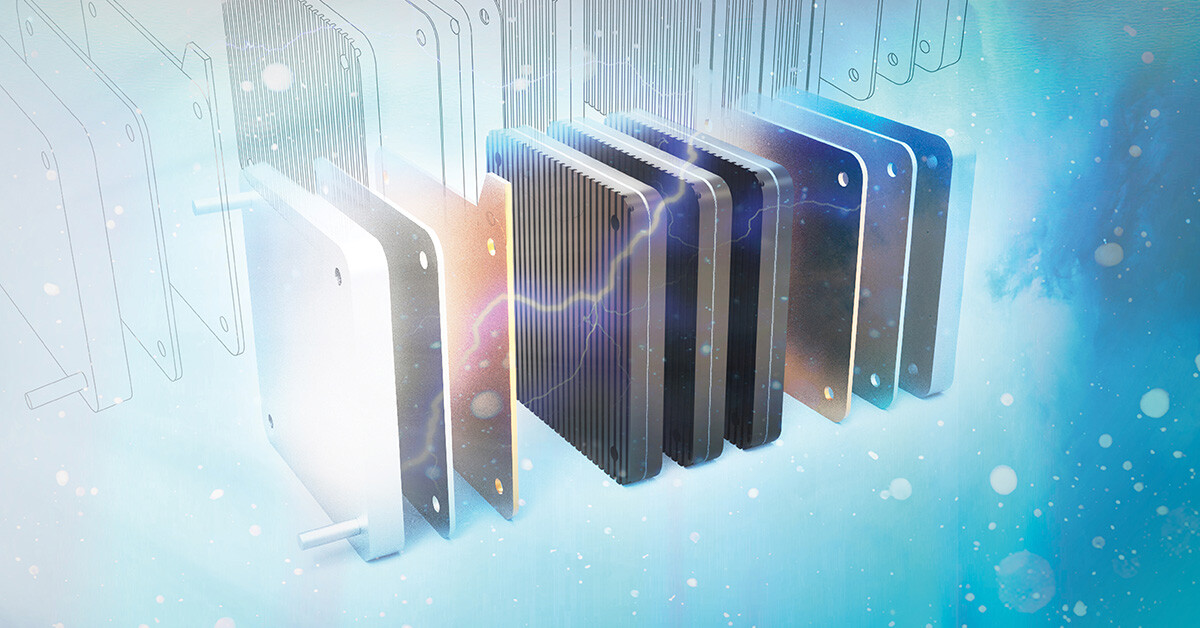
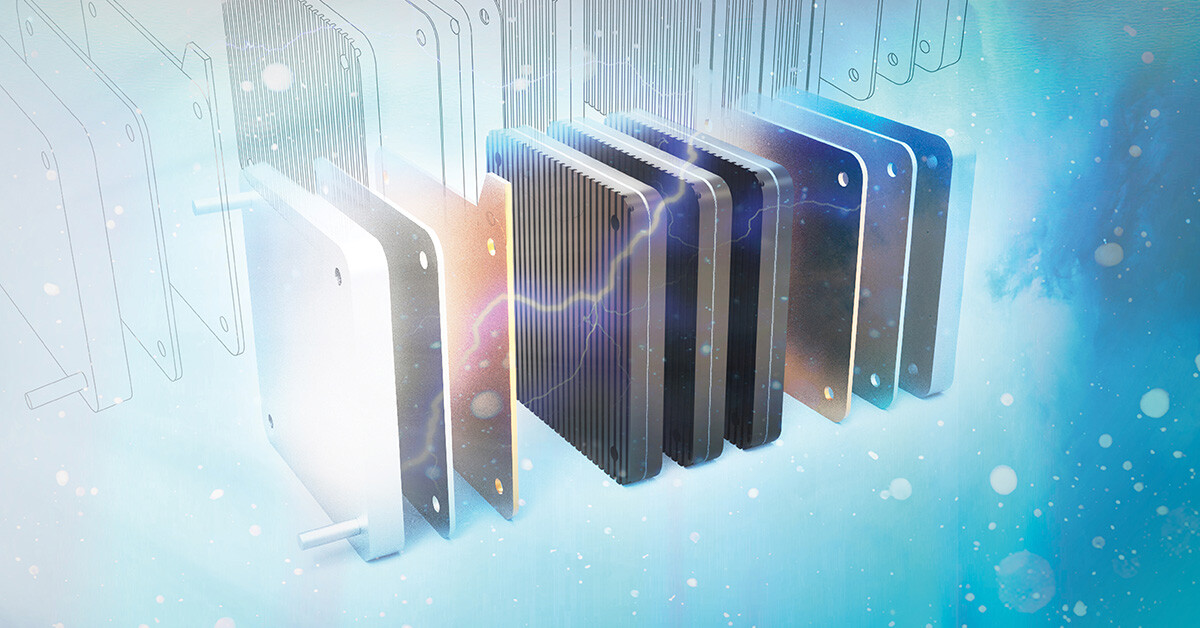
Decal Transfer Technology: The Key to Optimising Fuel Cell Performance and Reducing Waste
As the emphasis on fuel cell efficiency grows, it is essential to enhance their performance and competitiveness against other energy sources. This involves optimising the design and materials used as process aids and in components used.
For example, optimising the membrane electrode assembly (MEA) while minimising material waste in the pursuit of improving this clean technology.
Decal transfer technology is a manufacturing technique used to produce the catalyst coated membrane (CCM) within fuel cells and electrolysers. The MEA consists of layers, including a fluoropolymer electrolyte membrane sandwiched between catalyst-coated electrodes (anode and cathode). The process involves two mains teps: applying the catalyst to a substrate film and then transferring the dried catalyst layer to the membrane. The catalyst acts as a process enhancer, accelerating the reaction. While alternative methods like spray coating or direct coating exist, decal transfer is often the most effective approach for catalyst application.
How Does Decal Transfer Work?
Although we refer to this as a single process, it consists of two distinct steps:
- Applying the Catalyst: The first step involves bringing the catalyst ink or paste to the substrate. It's crucial that the substrate has high-enough surface energy; otherwise, it won't form a wet surface but will instead create isolated drops. A higher surface energy promotes better wettability, ensuring an even spread of the catalyst.
- Transferring the Catalyst Layer: In the second step, the crystalline catalyst layer adheres to the substrate. It is then pressed onto the membrane and the substrate gets peeled off afterwards, aiming for complete transfer with no residual material left behind. For optimal release during this transfer, a low surface energy on the substrate is desirable.
This presents a challenge since a high surface energy is needed for wettability in the first step and low surface energy is needed for effective transfer in the second step. There is only a small “window” of optimal surface energy to allow both wettability and transfer.
Our goal is to provide quality catalytic layer production solutions for CCMs. For instance, Versiv DF100 5 mil substrate achieves both requirements involved in the process: it has sufficient surface energy for wettability while also allowing for effective transfer. Other products in our range used as decal substrates include DF100 3mil, DF29NSP 67, CF103, and derivatives such as CF205, SRF103, and SRF205 — all of which serve as decal substrates.
Environmental Advantages of the Decal Transfer Method
From an environmental standpoint, decal transfer can offer significant benefits compared to spray coating. Spray coating can lead to uneven application of the catalyst layer, resulting in variations in performance across the MEA. It can also contribute to air pollution due to solvents and restrict human presence nearby during application.
Directly applied coatings may require longer curing times compared to decal transfer methods, slowing down production processes and reducing overall manufacturing efficiency. By contrast, decal transfer is more environmentally friendly and has some ecological benefits. As decal transfer allows for precise application of catalyst layers that can be thinner than those applied using traditional methods, the smaller volume of catalyst ink applied saves not only resources such as precious metals but also money invested.
The decal transfer process is repeatable, ensuring uniformity across each layer and leading to more consistent performance across fuel cells and electrolysers. The higher quality of our substrate surfaces enables thinner catalyst layers without risking shorts in performance. Ultimately, better surface quality translates into greater efficiency in final applications. The adhesion of directly coated layers may not be as robust as those applied via decal transfer, leading to potential delamination or failure during operation, which can compromise system integrity.
Mold Release and Cost Efficiency
During stacking of cells the components may not stick to the plates. The ease of releasing components from molds without residual materials minimises downtime during pressing of MEAs, further contributing to costsavings—an essential theme in selecting renewable energy materials, such as Versiv CL4 and CF205.
Future Potential of Decal Substrates and Catalyst Inks
Despite its advantages over rival technologies, there is still room for improvement in decal transfer technology. Future developments may focus on creating substrates with optimised surface properties that facilitate both wettability and transfer more effectively. This could involve new PTFE polymer formulations or PTFE coatings that enhance performance. Innovations in catalyst formulations could lead to inks that provide better adhesion, improved conductivity, and enhanced durability—further solidifying the benefits of this process. The more the whole equation is improved, the more often the substrate can be re-used.
Direct Coating Method (DCM)
In addition to decal transfer technology, it's important to consider direct coating methods (DCM), which have two main forms:
- Directly Coating the Membrane (Spray)
- Decal Transfer with Liquid Membrane Instead of Membrane Foil: Involves using a substrate (e.g. DF100 material), followed by electrode application (anode or cathode), liquid membrane casting, and then applying a second electrode before peeling off the substrate, again.
Given that context, decal transfer technology can offer significant advantages over direct coating methods in terms of precision, material efficiency, environmental impact, adhesion strength, and scalability. Thinner membranes lead to better efficiency in fuel cells; thinner catalysts reduce costs since precious metals are expensive while also benefiting environmental sustainability by minimising resource usage. These benefits make it a preferred choice for producing high-performance CCMs for fuel cell and electrolyser applications, ultimately contributing to improved sustainability and ecology in clean technology development.