PTFE release for surface quality in wind energy blade manufacture
The manufacturing process using Versiv components involves integrating PTFE-coated fabrics and tapes to create effective release liners. These materials are designed to withstand the rigors of production while providing superior performance in preventing adhesion and ensuring high-quality surface finishes.
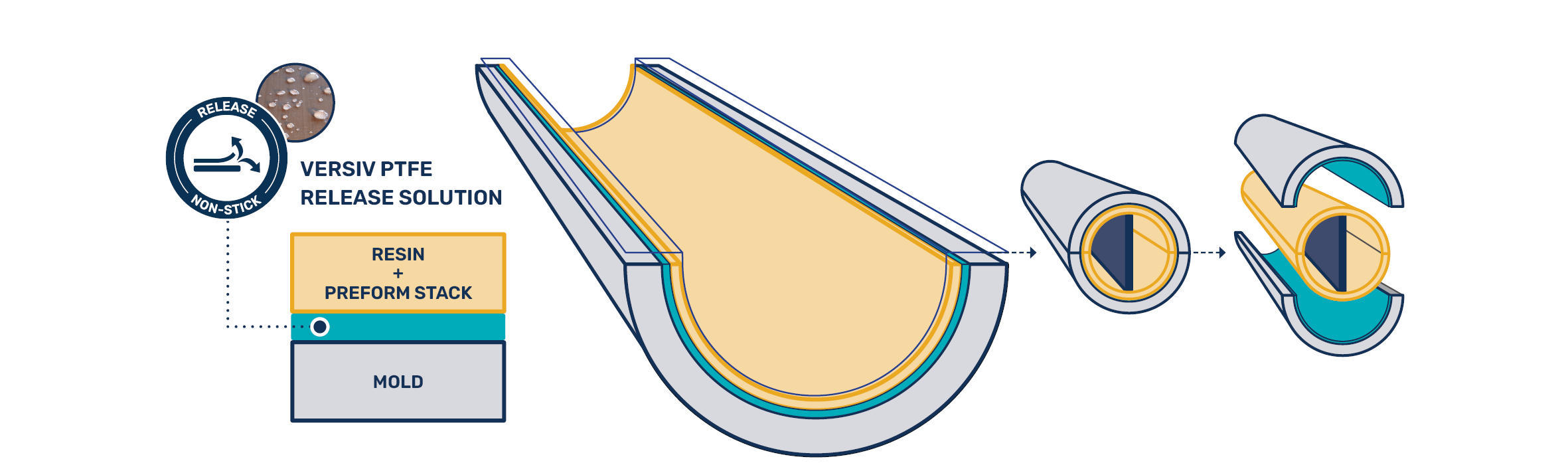
The enormous forces and temperatures during composite moulding processes put high stress on moulds, parts and materials. Versiv CLPSA 4 is a laminated PTFE-coated fabric, design to withstand this challenging environment.
Versiv CLPSA 4 S is a reusable and durable substitution for messy waxes and sprays. It allows for defect-free products with higher quality surfaces, reducing the need for further processing.
The silicone pressure adhesive layer added to one of its sides ensure that it stays in place while protecting and prolonging the life of the mould and tooling.