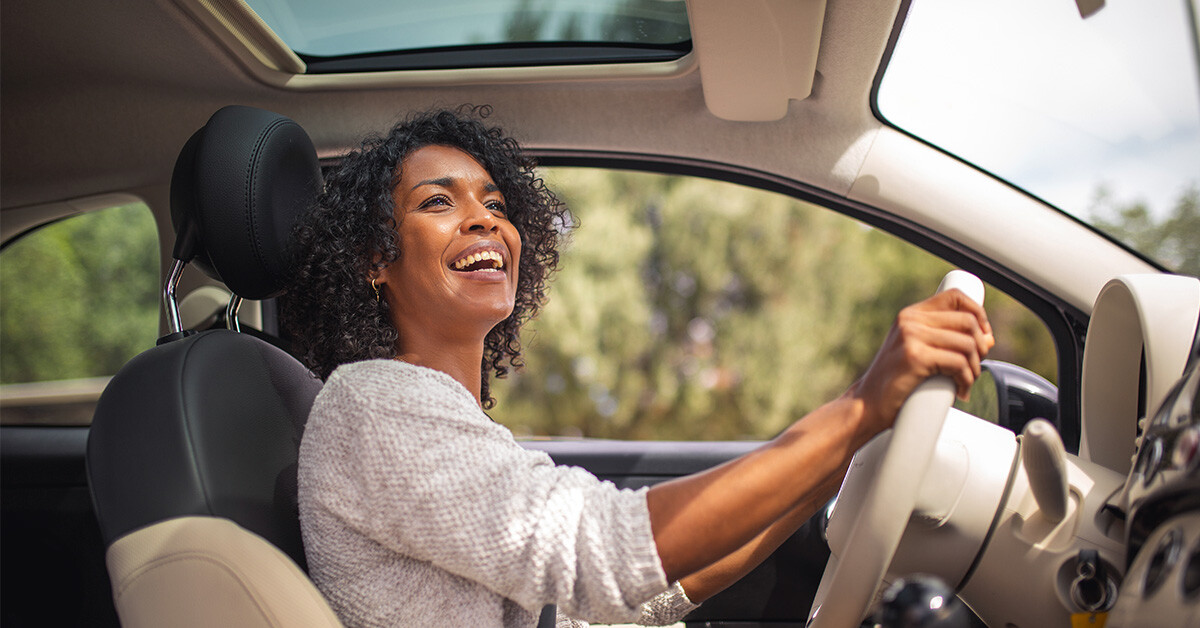
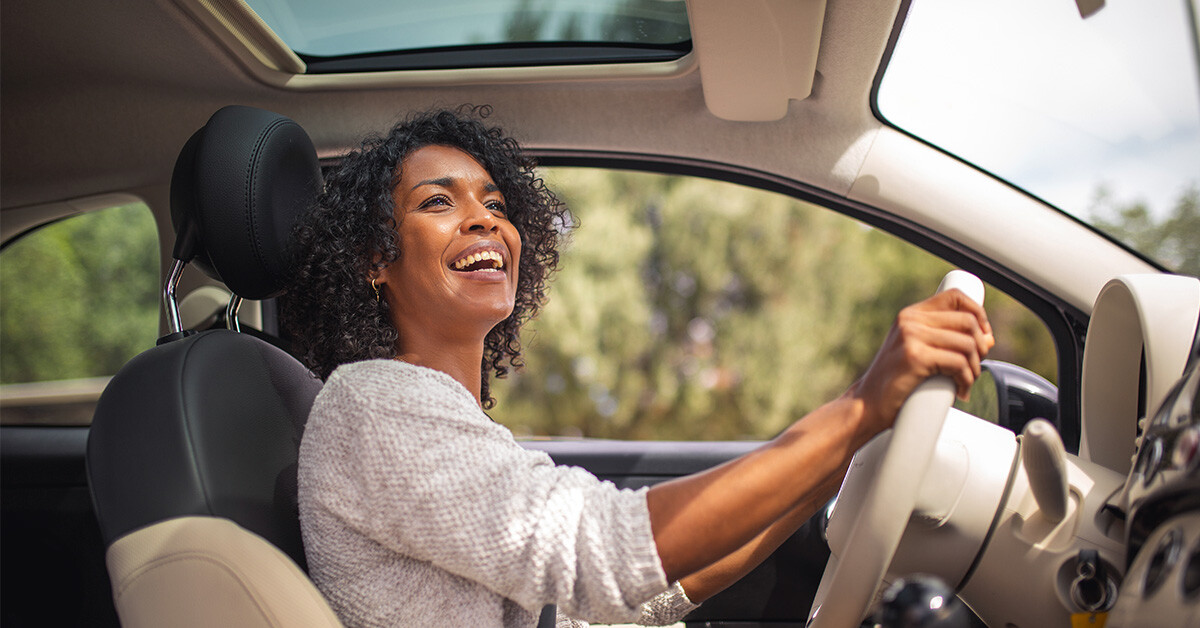
Low friction linings influence efficiency, extended lifetime and performance
Low friction liners are a composite of fluoropolymer and reinforcing material required in components such as electromagnetic solenoids, actuators, sliding roof systems, and printer fuser roll pressure pads. In the automotive sector, they are essential, particularly in brake systems, air suspension systems and transmission control units. They contribute to improved fuel efficiency, better overall vehicle performance, reduced wear on components, enhanced safety, and a smoother driving experience, based on their low friction nature. Within the industrial segment, they are well known and used in printer applications assuring consistent paper movement while reducing energy needs.
What benefits do low friction linings provide to automotive vehicles?
Within vehicle and industrial applications, low friction linings make devices more energy efficient by reducing the level of abrasion. Their use means more consistent movement forwards and backward, requiring less energy, with minimum hysteresis or "slip-stick" effects. In specific applications, it minimises the noise level generated by movement and performs consistently even at temperatures up to 200°C or higher throughout the device's lifetime.
Key properties of low frictionlining materials and their advantages
A low friction or moulded friction lining is a composite of different films such as fluoropolymer (typically PTFE) and reinforcing materials that acts as a linear glide-bearing surface. It provides reliable low-friction properties over many cycles, even at elevated or freezing temperatures, with minimum impact in terms of extra thickness or added weight.
The materials offer a variety of beneficial properties other technologies are unable to provide to date. They are a lightweight, flexible alternative to metallic and polymeric coatings and, in some cases, even rigid bearings that enable weight and space savings. In some cases, these LFLs result in longer-lasting performance and more economical solutions than nickel or chrome-plated parts.
These products are an essential alternative for design engineers and can replace messy greases, oils or lubricants that will wear out or need frequent "topping-up". They can also replace metallic coatings such as electroless nickel or chrome that are expensive and difficult to acquire inconsistent quality. They can be used instead of polymeric coatings such as PTFE on steel that are difficult to apply and often ‘consumed’ before the device reaches expected lifetime. Essentially, the polymeric alternative is less effective as it doesn’t stick as effectively to the base.
Low Friction Linings are an alternative to other polymeric bearings, such as polypropylene or polyamide, which have limited application range. They are also restricting design features due to the nature of the base polymers. When applications require low friction performance at elevated temperatures, minimum hysteresis or noise generation, and long-term compatibility with oils and chemicals, Versiv Linings are an excellent option. Due to their chemical base, sometimes the sole option.
Collaborate to develop tailored Low Friction Lining solutions
Versiv Low Friction Linings (LFL) are used in any application where reducing friction and wear is important for improving performance and extending the life of equipment. The ability to co-partner and tailor products to meet specific requirements, such as high electrical insulation or static dissipation, provides a flexible solution in designing many electro-mechanical parts. Contact us at Versiv Composites to find out more.