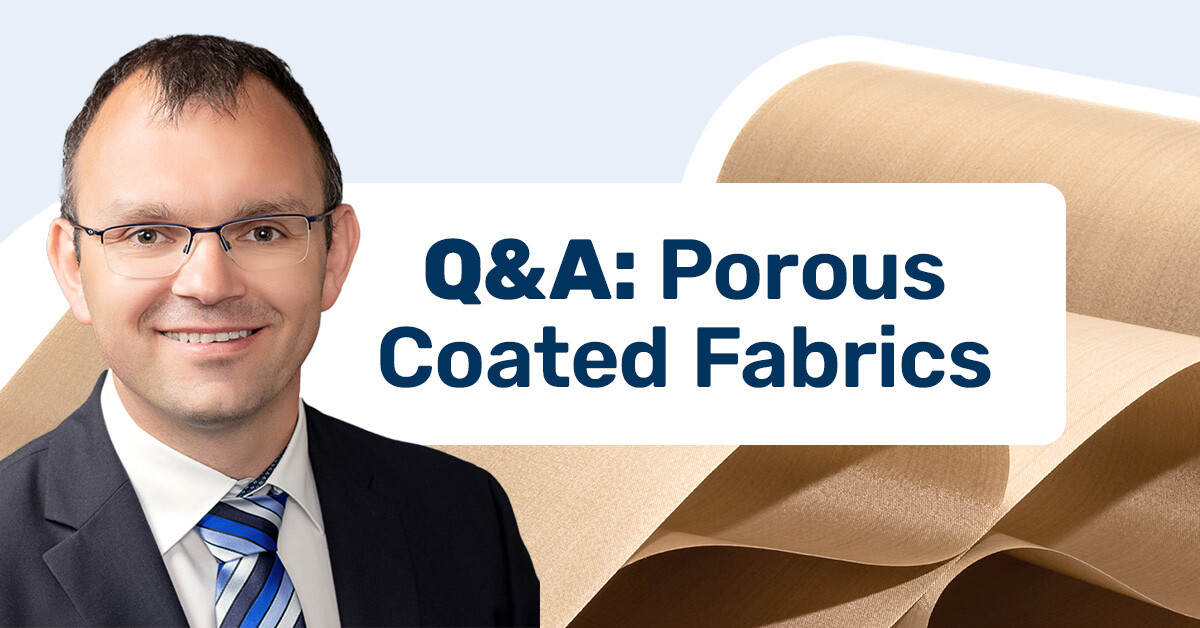
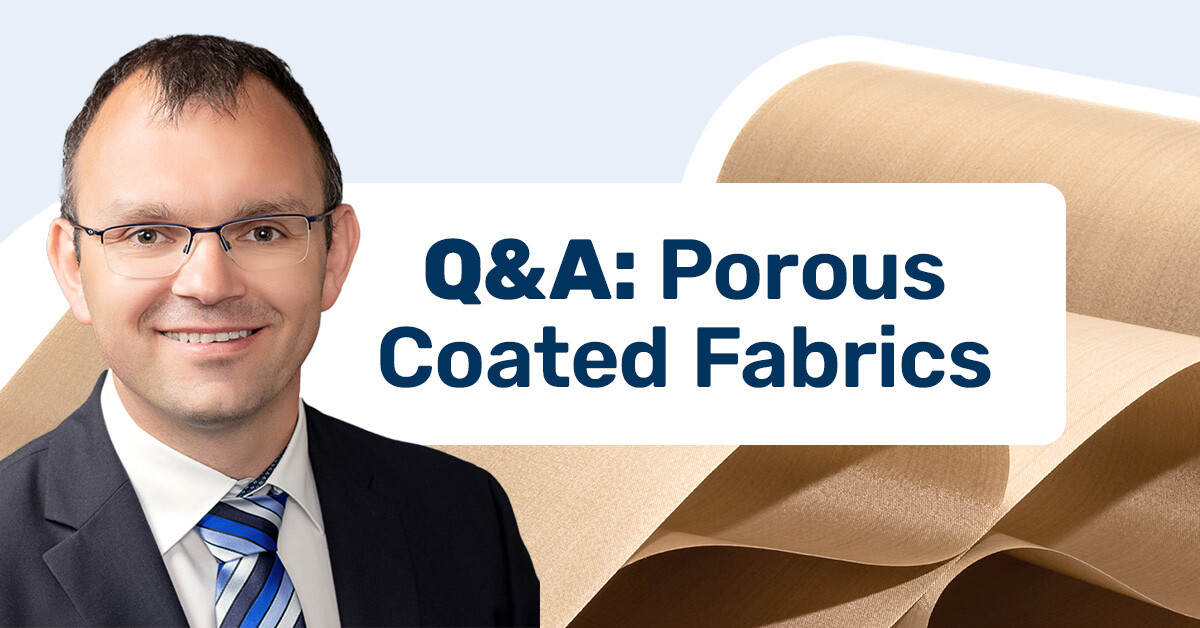
Innovations in Porous PTFE-Coated Fiberglass Fabrics
This week we caught up with Michael Katzer, Global Business Development Manager Automotive and Distribution, at Versiv Composites to talk about porous PTFE coated fabrics.
- What are the most common issues encountered when ensuring consistent porosity and airflow in PTFE-coated fiberglass fabrics, and how does Versiv address these challenges?
Ensuring consistent porosity and airflow in PTFE-coated fiberglass fabrics typically involves challenges related to the selection of the appropriate base fabric and the accuracy of the PTFE coating application. It's crucial to apply just the right amount of PTFE to maintain a high consistency in the fabric's texture and performance. Versiv addresses these challenges by carefully choosing the base fabric and then applying the PTFE coating to ensure optimal performance. A recent case highlighted the need for customisation based on choice of fabric, specifically for a unique foaming application. We are committed to tailoring solutions to meet specific industry needs.
- How do you manage the balance between chemical inertness and the need for customised surface treatments in PTFE coatings?
Versiv coated fabric materials inherently provide chemical inertness, which is a core advantage in maintaining the quality and stability of both the PTFE coating and the underlying glass fabric. This chemical inertness ensures that the fabric remains unaffected by various chemicals, therefore preserving its mechanical and core stability, even when customised surface treatments are applied to meet specific needs.
- How do you collaborate with clients during the design and development phase to ensure that customised PTFE-coated fabrics meet their exact specifications and performance expectations?
The collaboration process with clients involves starting with existing samples and engaging in a rigorous trial and error process. This approach helps to closely observe the behaviour of specific components, such as driving belts, under different conditions. The development process, which can span years, relies heavily on immediate feedback from clients. This is evident in, for example, the development of a serial belt for composite molding, where there is a collaborative and iterative approach to meet exact specifications and performance expectations.
- Given that the CF90 series is thermally stable from -150 to +260 °C and chemically inert, in what applications is this most beneficial, and why?
CF903 thermal stability and chemical inertness make it exceptionally well-suited for applications such as composite molding, where it serves as an effective breather material, and in aerospace composites. Its properties are also advantageous in MRI scanners and drying belts, where controlled airflow and temperature stability are critical. The material's ability to operate effectively across a wide temperature range while remaining chemically inert underlines its utility in these high-precision applications.
- How does the excellent heat transfer capability of the CF90 series benefit specific processes, such as heat sealing or curing?
The excellent heat transfer capability of CF903 is primarily attributed to its thinness, which prevents the formation of temperature barriers and enhances heat conduction. This feature is particularly beneficial in processes such as curing, where efficient heat transfer is crucial for achieving consistent and high-quality outcomes.
- In what specific advanced composites and molding processes is CF914-1 most employed, and why is it preferred over other materials?
CF914-1 is commonly employed in advanced composite and molding processes, particularly those requiring high-temperature performance and compatibility with demanding resins. Its preference over other materials is due to its temperature and chemical resistance, which make it capable of withstanding the rigorous conditions of high-temperature applications.
- What future developments or innovations do you foresee in the field of PTFE-coated fiberglass fabrics, and how is Versiv Composites positioned to lead these advancements?
Versiv is exploring innovative approaches such as replacing traditional hot water vapor foaming with infrared foaming. This development aims at achieving greater energy efficiency in the production of PTFE-coated fiberglass fabrics. This initiative can be influential in creating more sustainable and efficient fabrication processes.
Product
Description
No items found.