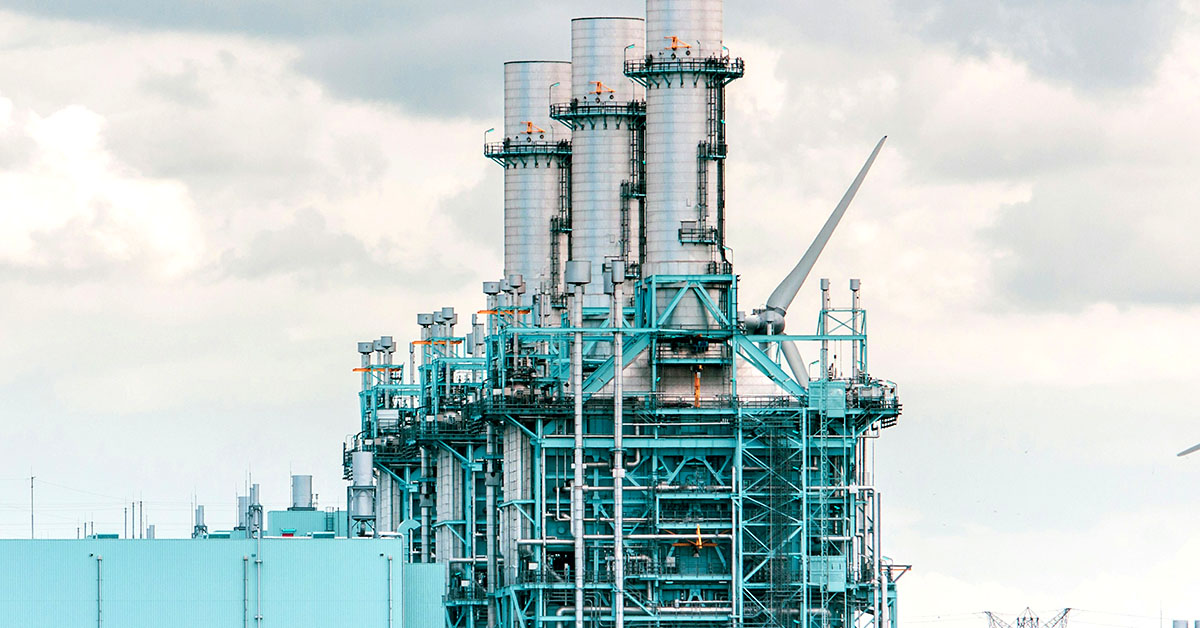
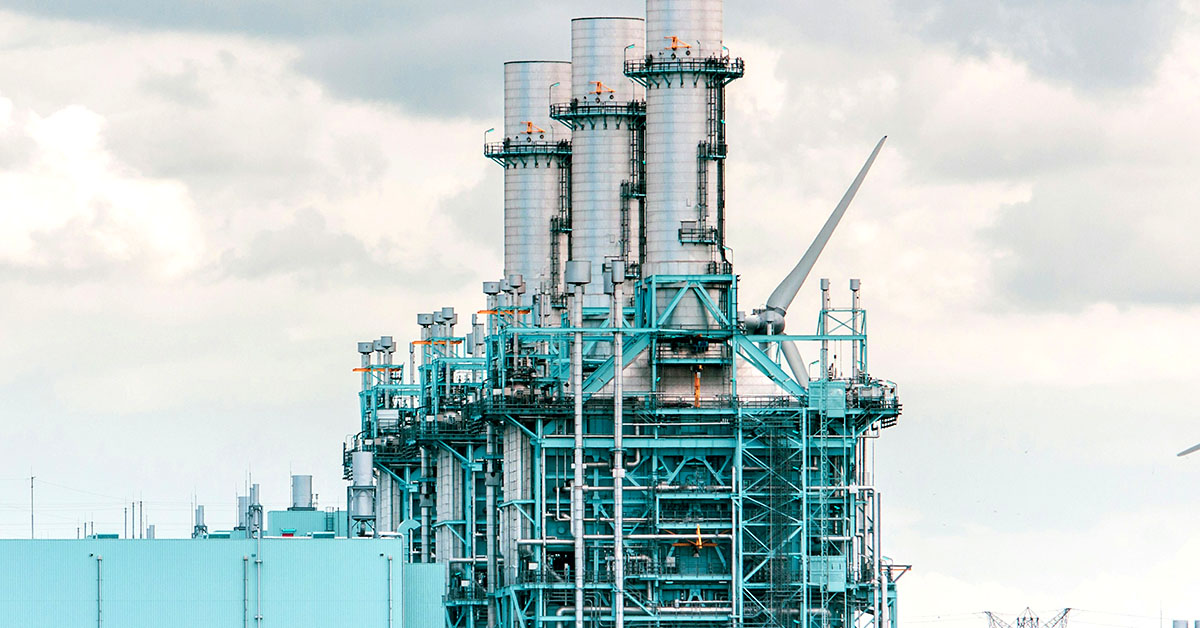
Maximising Power Plant Uptime: The Role of High-Performance Environmental Composites
High-performance environmental multimaterial composites are playing an increasingly crucial role in maximising power plant efficiency. These materials contribute through improving uptime and overall operational effectiveness. How are these materials making a difference in power generation?
The Importance of Uptime in Power Plants
Uptime is a critical metric in the power generation industry, directly impacting production, cost efficiency, and overall plant performance. Studies have shown that unplanned downtime can cost companies between hundreds of thousands of dollars or euros per hour.
Consistency around uptime is also essential for maintaining regulatory compliance, ensuring safety, and building a positive reputation in the industry.
Challenges in Power Plant Operations
Power plants face numerous challenges that can affect their uptime:
- Corrosive environments
- High temperatures
- Mechanical stress
- Chemical exposure
- Emissions control
Traditional materials often struggle to withstand these harsh conditions, leading to frequent maintenance, repairs and unplanned shutdowns.
Enter High-Performance Environmental Composite Materials
Versiv Flueflex Environmental Composites are engineered to address these challenges head-on. These materials offer a combination of properties that make them ideal for power plant applications:
- Extraordinary Strength Retention: Composites maintain their mechanical properties even in demanding environments, reducing the risk of unexpected failures.
- Superior Flexibility: This allows for better accommodation of thermal expansion and contraction, reducing stress on equipment.
- Chemical and Corrosion Resistance: Composites can withstand aggressive chemicals and corrosive environments, extending the lifespan of critical components.
- High-Temperature Resistance: Engineered to perform in extreme heat, these materials are perfect for use in various power plant systems.
- Gas-Tight Barrier Properties: This feature is crucial for preventing leaks and maintaining system efficiency.
Applications in Power Plants
High-performance environmental composites find applications in various areas of power plants:
- Flue Gas Desulfurization: These materials contribute to efficient removal of sulfur dioxide emissions from industrial flue gases, improving environmental compliance.
- Expansion Joints: Composites provide flexibility and durability in expansion joints, crucial for accommodating thermal movement in ductwork.
- Gas Turbine Systems: The versatility of these materials makes them valuable for improving performance, durability, and safety in gas turbine systems.
Benefits of Using High-Performance Composites
Implementing these advanced materials in power plants can lead to significant improvements:
- Increased Uptime: The durability and resistance of composites reduce the frequency of maintenance and repairs, maximizing operational time.
- Cost Efficiency: While the initial investment might be higher, the long-term benefits in terms of reduced maintenance and increased lifespan lead to substantial cost savings.
- Enhanced Safety: The reliable performance of composites in harsh conditions improves overall plant safety.
- Environmental Compliance: These materials aid in meeting stringent environmental regulations by improving emissions control systems.
- Competitive Advantage: Power plants utilising these advanced materials can achieve higher efficiency and reliability, setting them apart in the competitive energy market.
Here's a brief overview of each Flueflex Environmental Composite product, highlighting their chief properties and applications:
- FLUEFLEX 350 BF
Properties: High strength, excellent flexibility, and zero porosity with additional chemical resistance from PTFE film lamination.
Applications: Specifically designed for wet and dry flue gas conditions in flexible expansion joints, ideal for power plant emission control systems. - FLUEFLEX 350 BP
Properties: Similar to 350 BF but with PTFE film lamination on both sides for enhanced chemical resistance.
Applications: Suited for more demanding flue gas environments, particularly where exposure to corrosive chemicals is expected on both sides of the material. - FLUEFLEX 850 BF
Properties: Higher weight and thickness compared to 350 series, with excellent mechanical strength and zero porosity.
Applications: Designed for larger scale or higher stress flexible expansion joints in power plants and industrial facilities. - FLUEFLEX 1000 BF
Properties: Highest weight and thickness in the series, with exceptional tensile and tear strength.
Applications: Ideal for the most demanding flue gas environments, suitable for large-scale power plants and heavy industrial applications where maximum durability is required.
The Future of Power Plant Operations
In conclusion, high-performance environmental composites are proving to be highly influential in ensuring reliable power plant uptime. The unique properties of Flueflex Environmental Composites address many of the challenges faced by power plants, leading to improved efficiency, reduced downtime, and considerable cost savings.