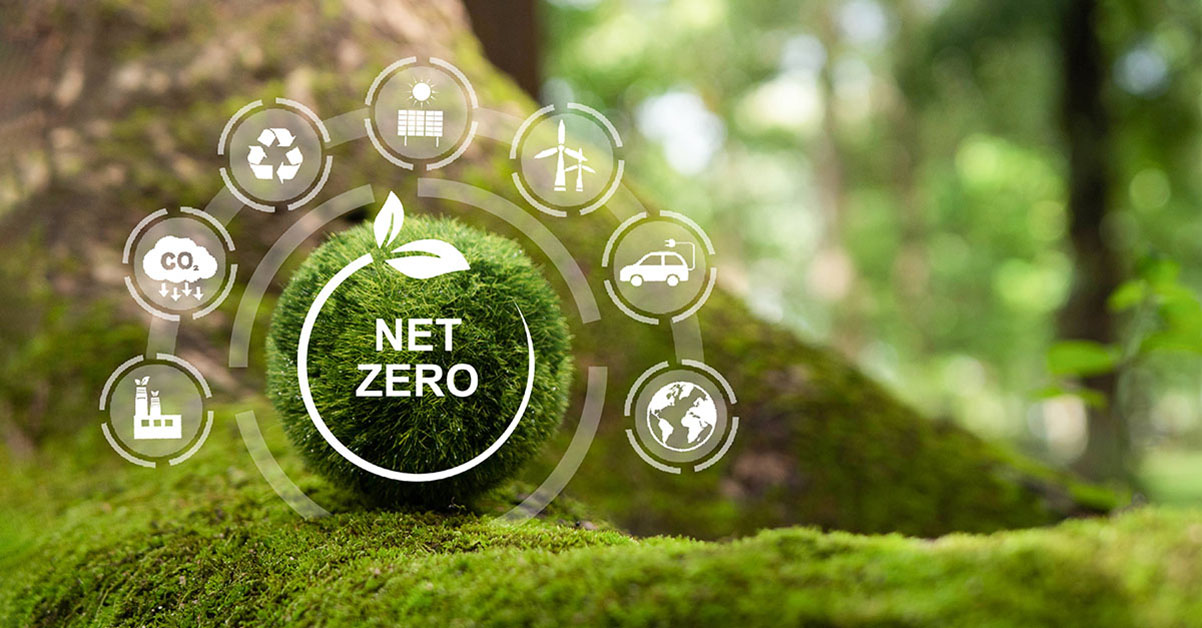
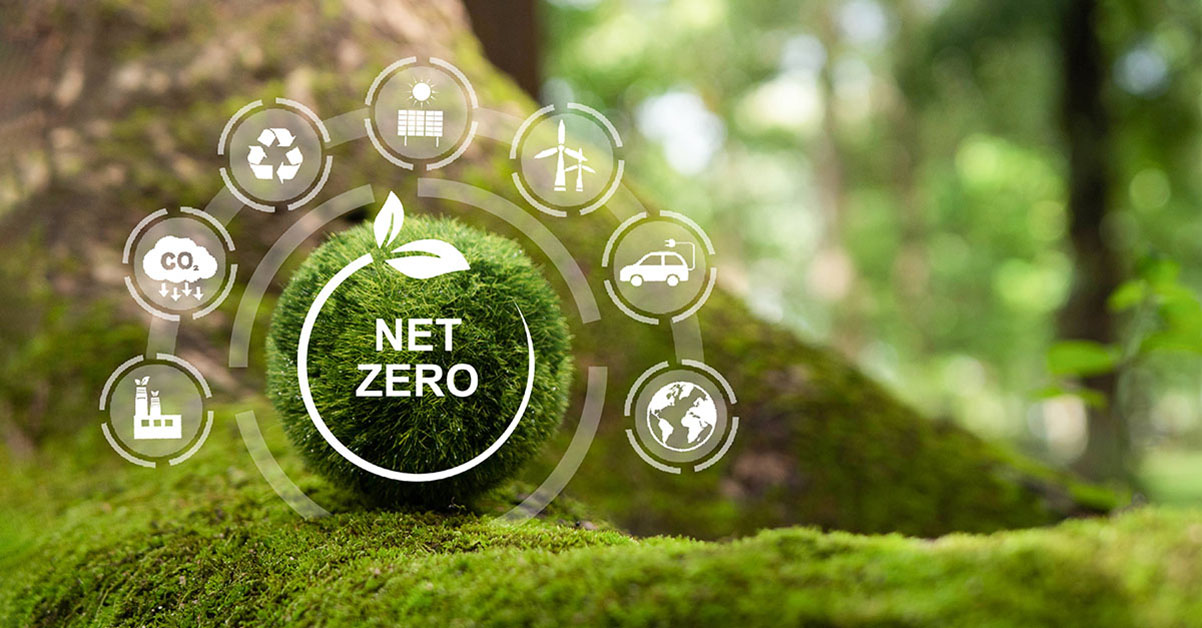
According to Climate Watch information released late last year manufacturing contributed 4 billion tonnes in CO2 emissions in 2020, with transport accounting for 5 billion tonnes of the total.Other sectors, such as electricity and heat proved to be the highest emitters,but construction, industry, agriculture, aviation and shipping all have work todo to reduce that output.
On this International Reducing CO2 Emissions Day, it is worth looking at what’s possible from the perspective of composite material manufacturing.
Renewable energy: Film and fabric solutions play an important part in the development of fuel cell and electrolyser manufacture as well as wind blades. These technologies are vital to meeting the requirement of a decarbonised energy sector. In fuel cells these materials are found in cells, seals and separators and other effective barrier solutions that can withstand temperature extremity.
The quality of the material also inputs, as it adds up to longer life spans in mechanical equipment. The materials are also key in catalytic layer production through their chemical resistance and durability.
Meanwhile, wind blade manufacture benefits from how the materials prevent adhesion and improve surface quality.
Environmental composites: These composite materials contribute to the efficient removal of sulphur dioxide emissions from industrial flue gases by providing flexible product for use in expansion joints. Flue gas desulphurisation is essential for multiple reasons, outside of emissions reduction, such as air quality improvement, prevention of acid rain and overall protection of ecosystems.
Automotive & Industrial applications: Low friction linings are a composite of fluoropolymer and reinforcing fabric required in components such as electromagnetic solenoids, actuators, sliding roof systems, and printer fuser roll pressure pads. The linings make devices more energy efficient by reducing the level of abrasion and the friction reducing properties of the materials ensure longer equipment life span.
In general, multimaterial composites often have a high strength-to-weight ratio. By using lightweight materials in the manufacturing of components, particularly in transportation (such as auto motive and aerospace), manufacturers can contribute to the overall reduction of vehicle weight. Lighter vehicles require less fuel or energy to operate, leading to lower fuel consumption and reduced emissions.
At Versiv Composites, we co-partner with our customers to develop solutions that can help to consistently curb emissions and help the world meet is obligations to planetary health.