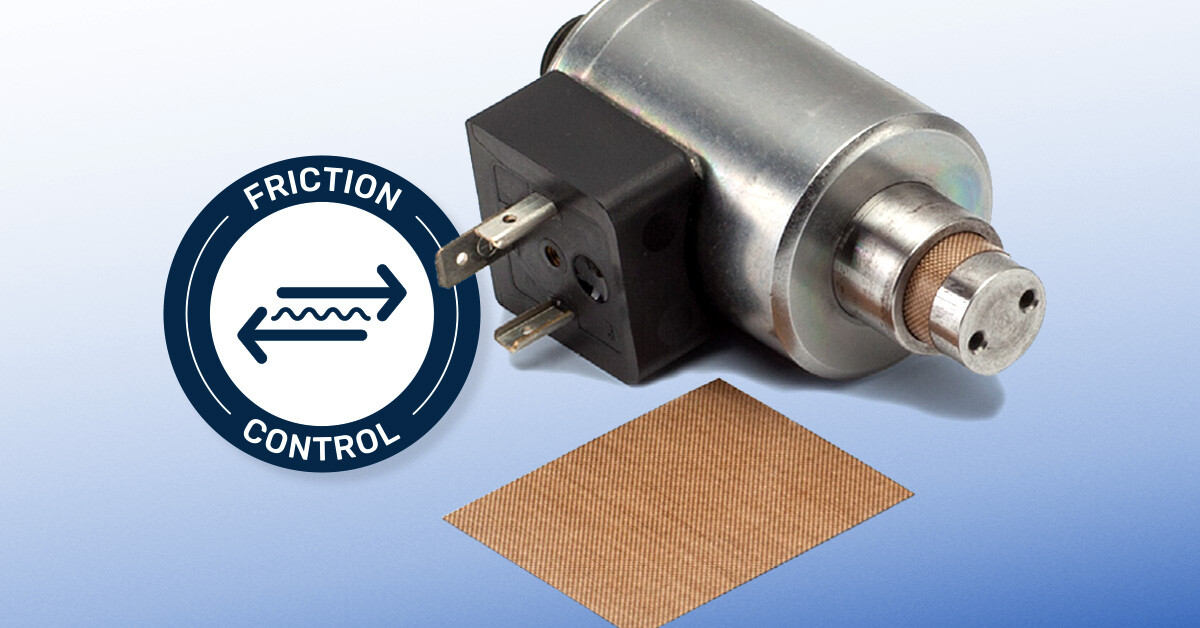
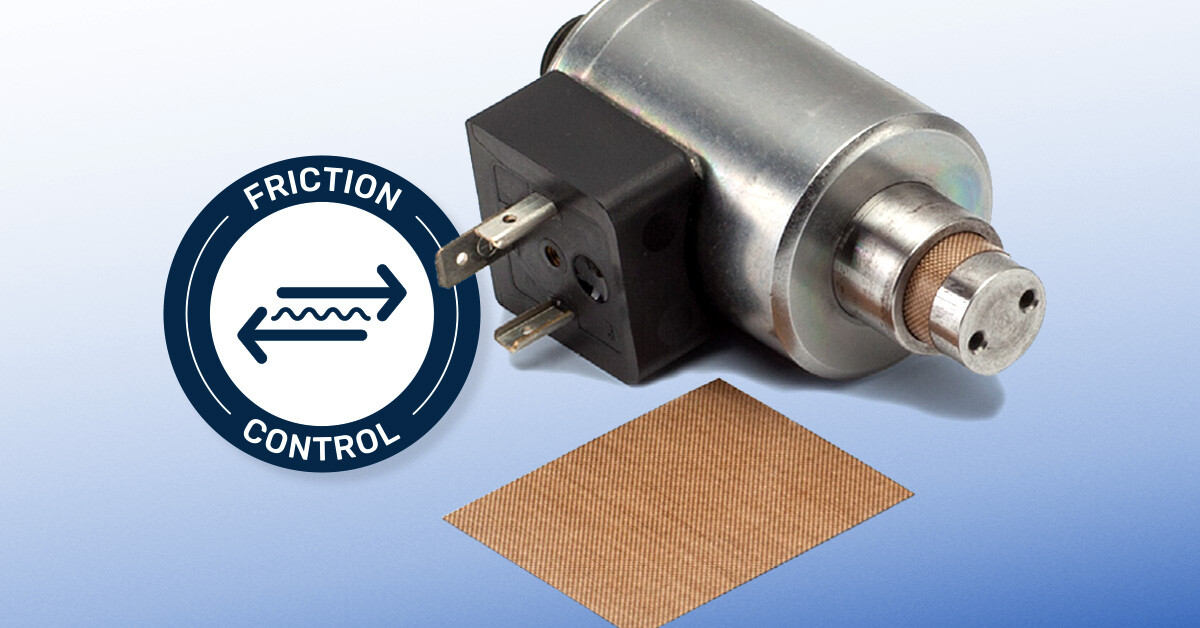
The significance of low friction linings (LFL) in the automotive industry is becoming increasingly pronounced due to advancements in technology and the growing demand for efficiency and sustainability.
LFL improve performance, reduce weight, and ensure compliance with stringent standards. At Versiv Composites, we are dedicated to developing high-quality LFLs that meet the evolving needs of automotive manufacturers.
1. The Importance of Thickness in Low Friction Linings
- Critical Specifications: Thickness is vital for ensuring proper fit within solenoids, directly impacting the efficiency of gear changes and hydraulic actuation.
- Precision Control: Versiv maintains a tolerance of ±5 microns, surpassing the industry standard of ±20 microns, ensuring consistent performance and reliability.
Thickness is a critical characteristic for our customers because the lining must fit into the solenoid. An armature moves within the solenoid when activated by a magnet, and maintaining proper clearance is essential for optimal performance. Important to note is that we talk about a system that is influenced by various components and therefore various tolerances. The armature is responsible for changing gears and actuating hydraulics or pneumatics, making thickness a significant factor in design.
Weight correlates directly with thickness; heavier products typically indicate greater thickness. Additionally, the surface quality is important; the coating must be smooth and free from all sorts of defects to ensure consistency.
We also evaluate other factors such as electrical performance or tensile strength. Curling can impact handling during assembly, especially when robots are involved. We perform thorough visual inspections to identify any faults, allowing us to flag issues for later review or skip problematic sections. Most of our material is supplied as slit tapes, which customers then stamp into their desired shapes. We are increasingly supplying stamped parts and can provide them as tapes or bundles coming from a fully automated system.
2. Rigorous Testing and Quality Assurance
- Comprehensive Testing Protocols: Our laboratory conducts extensive testing, including visual inspections and mechanical evaluations, to guarantee product integrity.
- Documented Compliance: We adhere to rigorous automotive qualification processes, including initial sample inspection reports and failure modes analysis.
For automotive clients, there's a rigorous qualification process that requires comprehensive documentation. This includes initial sample inspection reports, parts submission warrants, control plans, failure modes analysis, flow charts, and compliance criteria. At Versiv, our laboratory conducts physical testing, with a team of engineers and inspectors overseeing the process. We have dedicated resources for automotive projects, often dedicating one FTE a week in the lab to LFL projects alone.
As mentioned, thickness is critical, with an industry standard tolerance of ±20 microns. We achieve tighter tolerances of ±5 microns through careful coating processes that minimise defects. Although this method may not be the cheapest, it ensures high quality. For example, we use fabrics like CF105 for general applications and SP105J for automotive needs to meet stricter tolerances and lower defect levels.
3. Unique Advantages of Versiv Low Friction Linings
- Weight Reduction: Our LFLs can weigh as little as 0.2 grams compared to traditional bearings, enabling faster response times and reduced hysteresis.
- Enhanced Performance: By eliminating bearings, we allow for smaller solenoid designs without added weight, improving overall vehicle efficiency.
Our products are supplied to many premium automotive brands and our linings are essential for advancing industry standards.
For certification, our products meet ISO 9001 requirements and comply with the higher IATF16949:2016 standard crucial for the automotive sector.
4. Thermal Stability and Wear Resistance
- Robust Temperature Range: Versiv PTFE coatings perform effectively from -160°C to +260°C, unmatched by other plastics in the market.
- Durability Under Pressure: Designed for longevity, our products meet demanding specifications for automotive applications, including a lifespan equivalent to 300,000 km.
Thermal stability and wear resistance are key considerations in product specifications. For instance, if a customer requires a car to last 300,000 km, this corresponds to specific PTFE coating requirements. Our automotive products feature maximum PTFE coating for durability and longevity.
In terms of temperature resistance, our PTFE products can operate between -160°C and +260°C throughout their lifespan—conditions that few plastics can withstand while maintaining one of the lowest coefficients of friction available. We also offer lighter coatings for industrial applications like off-road machinery that may require” less precision and accuracy”.
5. Environmental Compliance and Safety Standards
- Adherence to Regulations: As mentioned, Versiv complies with ISO 9001 and IATF 16949:2016 standards, ensuring our products meet high automotive quality requirements.
- Sustainable Practices: We prioritise environmental safety by ensuring no harmful substances are present in our materials.
Regarding environmental compliance, we use glass fiber filaments sized to avoid respiratory issues; our filaments are larger than 3.5microns in diameter to mitigate these concerns. The stability of PTFE is another consideration; it is one of the most stable chemicals available. We also ensure that our suppliers do not use any prohibited substances related to PFOA or PFAS in compliance with environmental regulations.
As compliance requirements grow more complex, Versiv has increased resources dedicated to vetting incoming chemicals—monitoring their contents and ensuring environmentally friendly processing and disposal practices.
6. Innovation and Future Developments
- Ongoing R&D Efforts: With recent expansions in our R&D capabilities, we are committed to developing lighter, thinner linings that cater to the latest automotive trends.
- Market Leadership: As a leader in this niche market, Versiv is poised for continued growth with enhanced manufacturing and monitoring technologies.
Versiv leads in this niche market with expanded manufacturing capabilities and enhanced monitoring equipment for processes like in-line thickness checking and antistatic monitoring—all focused on low-friction linings (LFL).
While we primarily deal with coated fabrics reinforced with woven glass fiber, some customers prefer polyimide as a reinforcing material. A notable trend is that most solenoids operate at a thickness of 75 microns or even thinner; we now offer liners at just 50 microns thick, resulting in lighter and thinner options. Our recent R&D expansions will further enhance our ability to serve automotive customers over time.
Conclusion
Versiv low friction linings are used the automotive industry for applications such as brake systems, double clutches, other transmission systems, and roof blind sliding systems to reduce wear and hysteresis to improve performance. Low friction linings are also used in low friction bearings, gears, and other mechanical components to reduce friction and improve efficiency in industrial machinery and as bearing type material to optimise movement in printers.
Versiv Composites is at the forefront of low friction lining technology in the automotive sector. Our commitment to quality, compliance, and innovation ensures that we not only meet but exceed the expectations of our customers. Aswe continue to evolve with industry demands, we remain dedicated to providing solutions that enhance performance and sustainability in automotive applications.
Explore how low friction linings can enhance your solenoid design for improved efficiency and performance. Contact us for tailored solutions today.