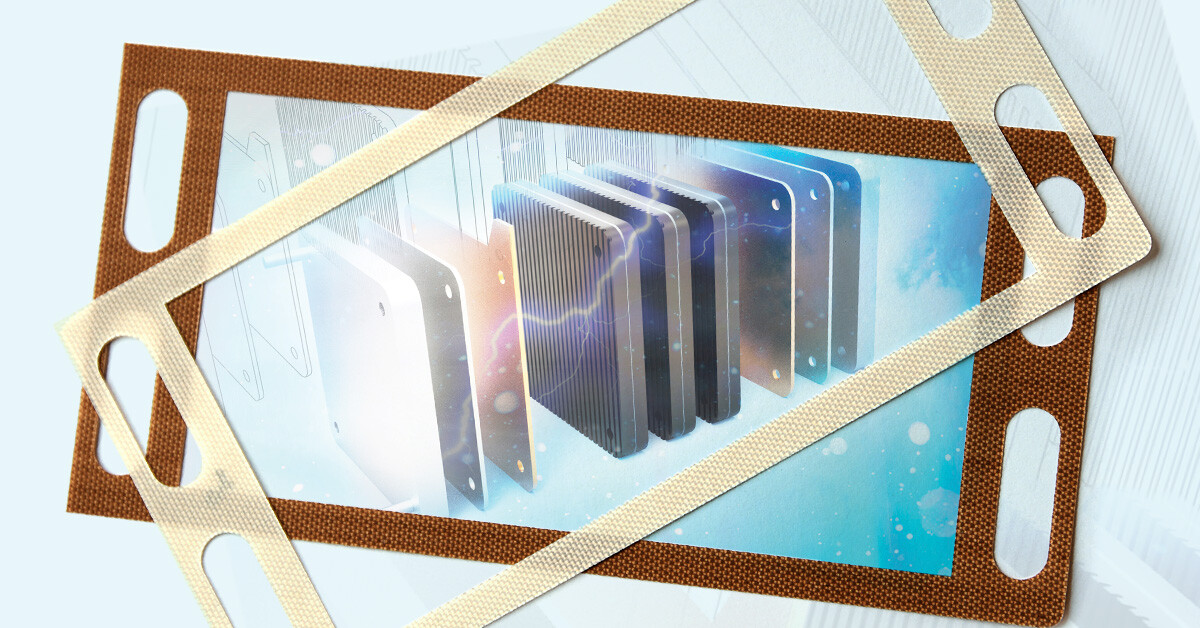
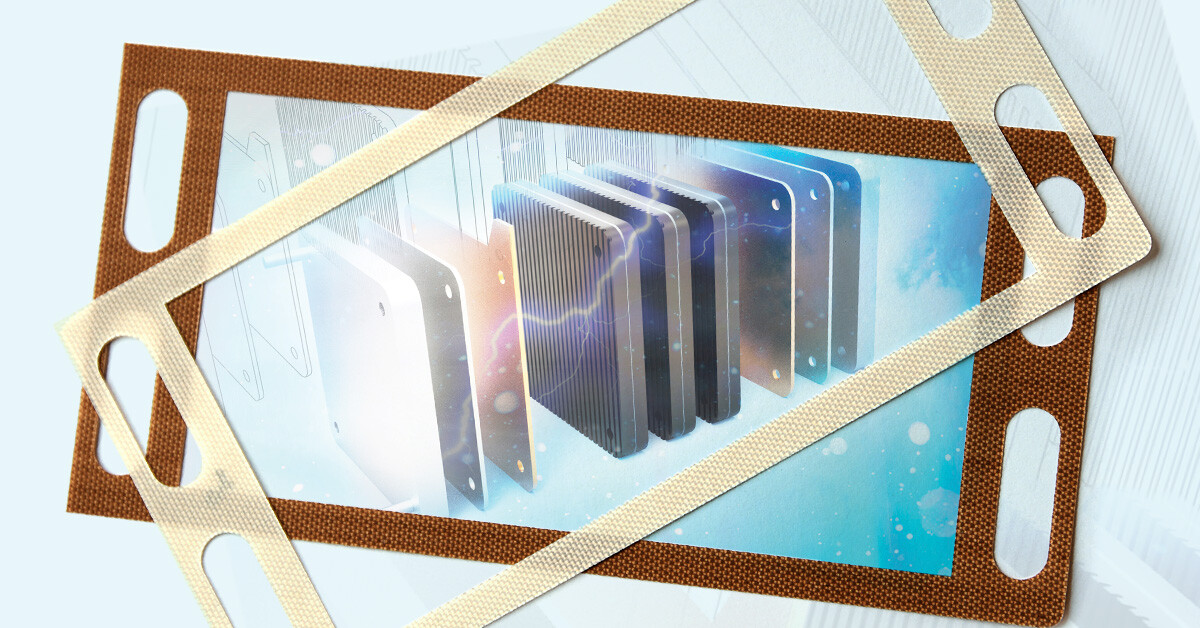
PTFE-based composite materials valuable input to fuel cell performance
Fuel cells have grown in influence in recent years as an exciting alternative energy technology, complementing the global need for renewable, high efficiency, low emission electricity. Polymer, or more specifically Polytetrafluoroethylene (PTFE)-based composite materials play a critical role in supporting fuel cell processes by providing essential functions such as gas diffusion, water management, corrosion resistance, thermal stability, sealing, and electrical insulation. Given the qualities hydrogen fuel cells can offer as a decarbonisation solution, it looks likely that the tech is set to grow significantly in the coming decades.
If fuel cells are to proliferate successfully, composite materials like coated films have a key role to play in enhancing cell lifetime, and the prospect of hydrogen energy making a genuine impact.
Boosting the lifetime of fuel cells
Composite membranes such as coated films play a critical role in extending the lifetime of fuel cell structure, especially in the gaskets used in the technology, and during the decal transfer process. Ensuring long lifetime is important in terms of economic viability, and overall reliability and sustainability of fuel cell technologies. Pure PTFE and PTFE-coated gaskets make for a longer lifetime and reduce the need for frequent replacements, with lower lifecycle costs in the long term.
How coated films support fuel cell applications
Within fuel cell and electrolyser gaskets, Versiv films can be used to protect graphite bi-polar plates in fuel cells. The films help to increase the durability and stability of the bi-polar plate by protecting it from corrosion and other forms of degradation. This leads to longer lasting, more efficient fuel cells.
Coated films can be used as a substrate or carrier during the Decal Transfer Method (DTM). The coated film materials are ideal for the process as they provide smooth and homogenous surfaces and very tight thickness control. It means the coating process can be optimised during the DTM, resulting in very thin catalyst layers, improving the efficiency of the MEA and the overall stack. The used surface energies allow both wettability and release.
The films are also ideal for customised fuel cell and electrolyser solutions as they can be further processed by various techniques such as stretching, laminating, or surface treating to enhance its properties for specific applications.
In addition, monolayer films enhance the performance of fuel cells, irrespective of the most stressful and challenging conditions. This includes working at high pressures and temperatures of up to 300˚C (572˚F) and in harsh chemical environments.
PTFE-based composite materials have excellent thermal resistance, ensuring fuel cells can withstand the high temperatures involved without compromising structural integrity over extended periods of time.
By helping to maximise fuel cell performance and longevity, these solutions contribute to their wider usage, both as components and as process aids.
Next steps for interested parties in fuel cell composite materials
Need a deeper perspective on how Versiv Composites can positively impact efficiency, reliability and durability of fuel cell systems? Contact our team or read more in our resources area – including our fuel cell and electrolysers brochure.