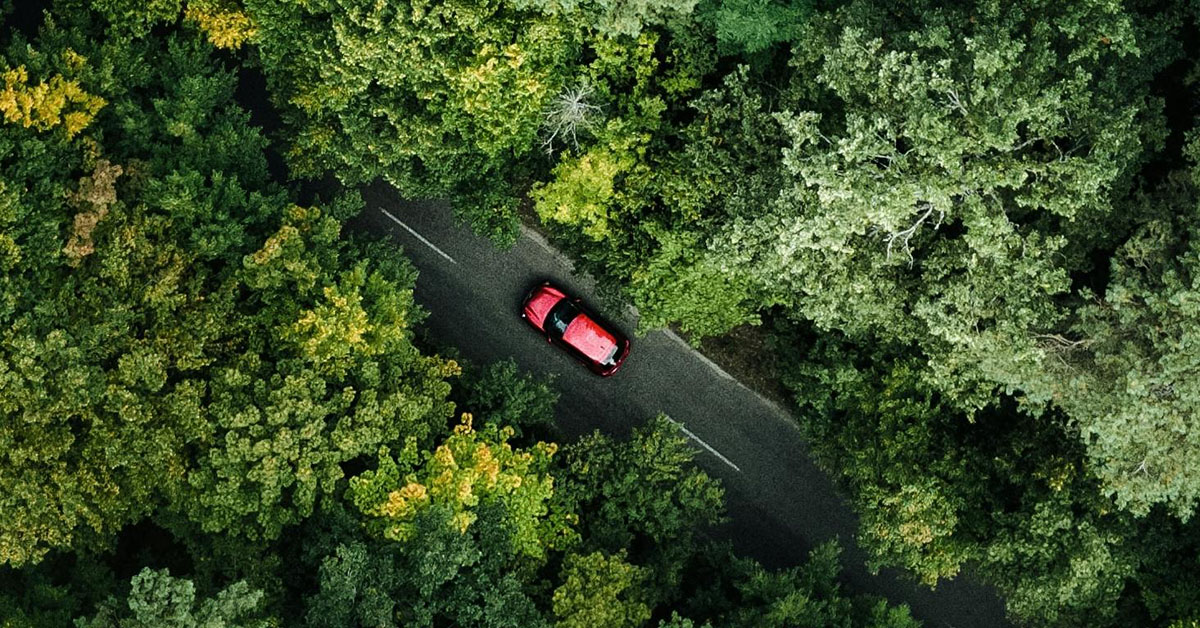
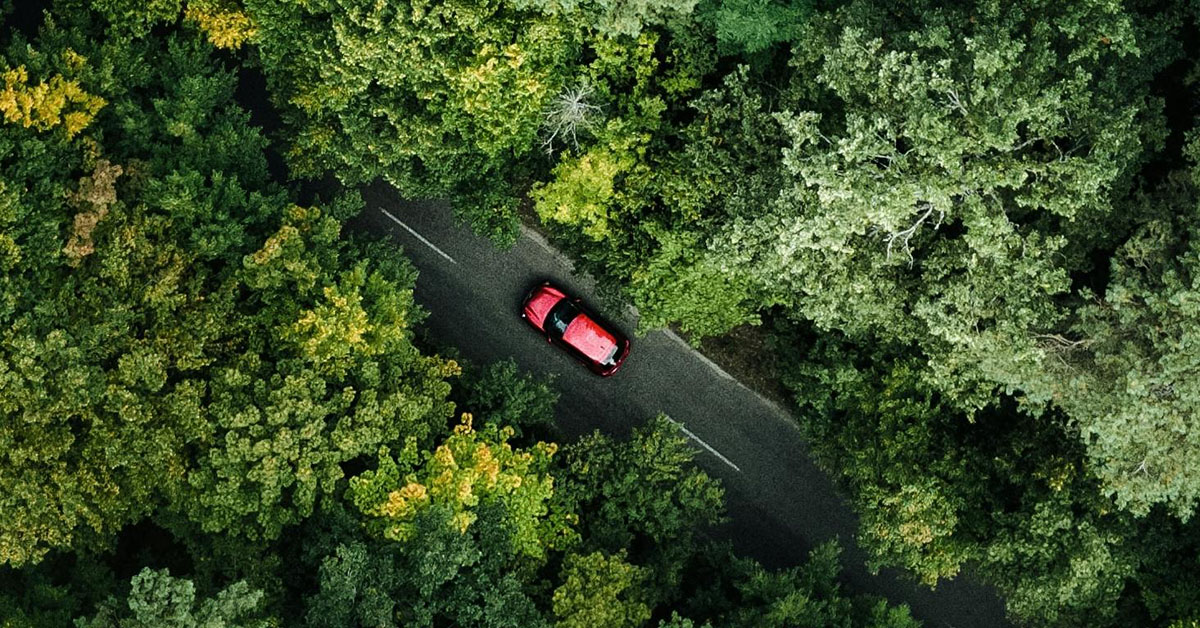
The race is on for a cleaner, greener future, and the automotive industry is shifting gears towards sustainable solutions. One such solution: low friction linings (LFL), composed of innovative composite materials. This blog dives into how these friction fighters are revolutionising the automotive landscape, reducing CO2 emissions and propelling us towards a low CO2 mobility future.
Low Friction Linings – a powerful offering:
Imagine a car that stops effortlessly while simultaneously saving you fuel and reducing your environmental impact. That's the impact of low friction linings. Traditionally, friction linings were clunky and heavy, and reliant on metals. But composites offer a lighter, more efficient alternative.
Shifting Gears with Composite Advantages:
- Lightweight Champion: Composite linings shed pounds compared to traditional materials. This translates directly to increased fuel efficiency and lower CO2 emissions. Every gram counts when it comes to a car's environmental footprint.
- Performance Pit Crew: Don't be fooled by the weight loss. Composites can be engineered to withstand extreme temperatures and wear, ensuring optimal braking performance and durability.
- Sustainable Steward: Many composites are crafted from recycled or renewable materials, aligning perfectly with the industry's push for eco-friendly solutions. This closes the loop on resource usage and promotes a circular economy.
- Customisable Craftsmanship: Unlike their one-size-fits-all counterparts, composite linings can be tailored to specific vehicles and driving conditions. This customisation ensures optimal performance for every driver, from city commutes to high-performance tracks.
Automotive low friction linings also play a crucial role in enhancing the performance and reliability of various systems in automated driving, including automatic gearboxes, Advanced Driver Assistance Systems (ADAS) & car sunroofs. Here’s how LFLs contribute:
1. Automatic Gearboxes
- Enhanced Efficiency: Low friction linings reduce the internal resistance in automatic gearboxes, leading to smoother and more efficient gear shifts. This efficiency is crucial for automated driving, where precise and reliable transmission performance is required.
- Reduced Wear and Tear: By minimising friction, these linings help reduce wear and tear on gearbox components, extending their lifespan and reducing maintenance needs. This reliability is vital for the consistent performance expected in automated driving systems.
2. Advanced Driver Assistance Systems (ADAS)
- Sensor Reliability: ADAS systems, including Lidar, rely on accurate and timely data to function correctly. Low friction linings can contribute to the smoother operation of moving sensors, ensuring that data is collected without interference from mechanical noise or wear-related issues.
- Dielectric Material Improvements: In ADAS systems, dielectric materials are used in various sensors and electronic components. Composite materials can help improve the performance and longevity of these materials by reducing the mechanical stresses and thermal buildup that can degrade dielectric properties over time. This ensures better signal integrity and more reliable sensor performance.
- Enhanced Actuator Performance: Many ADAS features involve actuators for tasks like steering, braking, and throttle control. Low friction linings in these actuators can ensure smoother and more precise movements, which are critical for the safety and effectiveness of automated driving systems.
3. Car Sunroofs
- Avoiding Grease Usage: Traditional sunroof mechanisms often require greases to reduce friction, which can attract dirt and degrade over time, leading to increased maintenance. Low friction linings provide a cleaner alternative by inherently reducing friction without the need for lubricants.
- Smooth Operation: Low friction linings ensure that sunroofs open and close smoothly and quietly. This is particularly important in the context of automated driving, where a seamless user experience is paramount.
- Durability and Longevity: By reducing wear on moving parts, these linings help maintain the functionality of sunroofs over longer periods, aligning with the durability expectations of modern automated vehicles.
Additional Benefits for Automated Driving
- Fuel Efficiency: By reducing friction in various mechanical systems, low friction linings contribute to overall fuel efficiency. This is especially beneficial for hybrid and electric vehicles, where efficiency gains are directly translated into extended range and reduced energy consumption.
- Heat Management: Reduced friction leads to less heat generation in mechanical components. This is crucial for maintaining optimal operating temperatures, which can enhance the performance and longevity of electronic systems in automated driving vehicles.
- Enhanced Safety: Reliable and consistent operation of gearboxes, ADAS, and other systems supported by low friction linings contributes to the overall safety of automated driving. Any reduction in mechanical failure risks directly translates to safer vehicle operation.
Navigating the Challenges of Composites
While composites offer a compelling path forward, there are hurdles to address:
- Manufacturing Maze: Crafting composites can be complex, requiring specialized equipment and processes. This can translate to higher upfront costs and longer production times.
- Material Matters: Striking the right balance of strength, flexibility, and heat resistance is crucial. Inconsistent material properties can lead to performance and reliability issues if not engineered correctly.
- Cost Considerations: The initial price tag of composites might be higher than traditional materials. However, long-term savings from improved fuel efficiency and reduced maintenance can offset those costs.
- Recycling Roadblock: The intricate nature of composites makes recycling a challenge. Developing effective recycling methods is critical to maximize their environmental benefits.
Green Light for the Future
Despite these challenges, the potential of low friction linings is undeniable. Continued advancements in manufacturing, material science, and recycling are paving the way for a smoother, greener future.
Collaboration is Key: Open communication between automakers, material scientists, and policymakers can accelerate the adoption of composites. Working together, we can unlock the full potential of low friction linings and steer the industry towards a sustainable future.
Check out our Low Friction Linings Brochure and contact our team for more information!