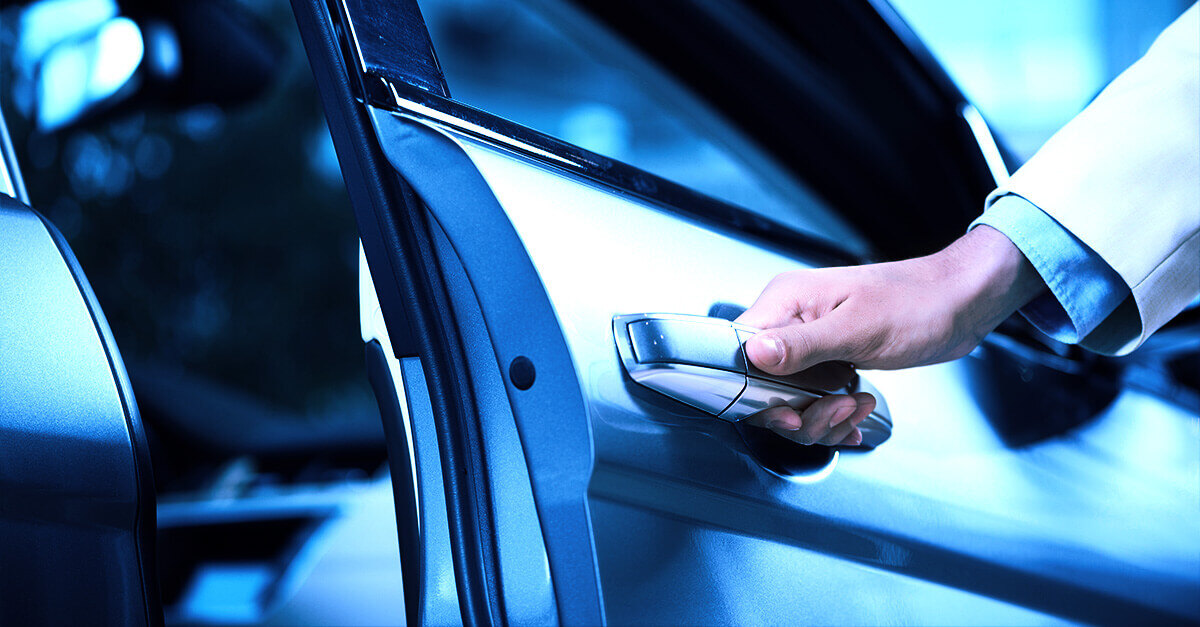
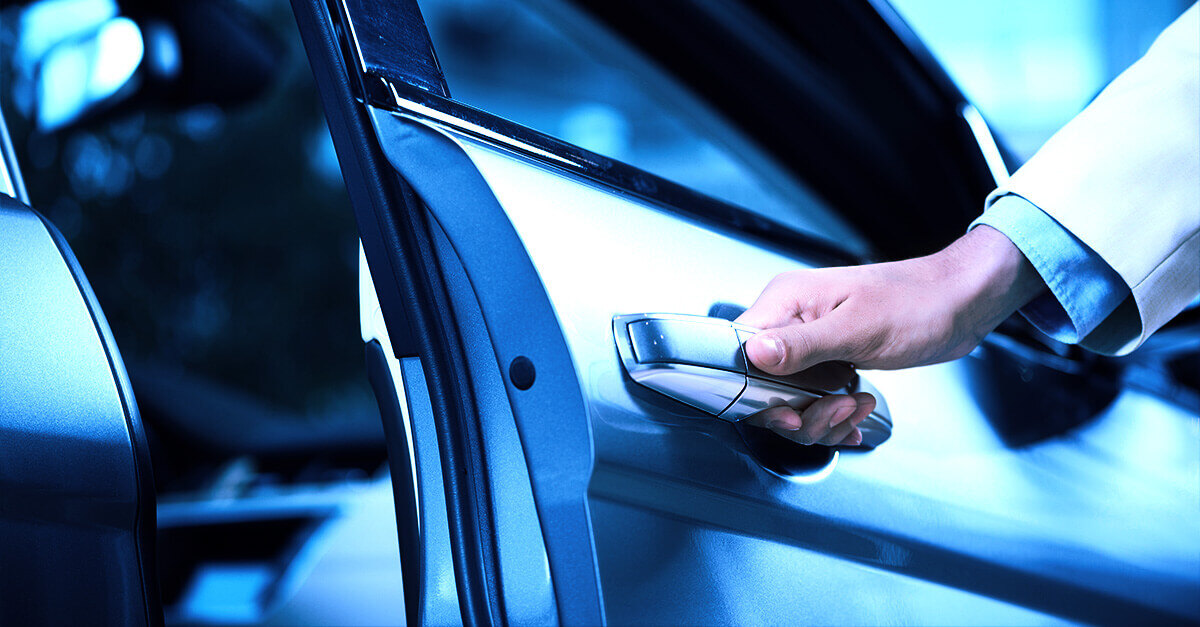
Driving into the Future: Fluoropolymer Materials in Automated and Connected Vehicles
After many years of progressive improvement in its mechanical features - car body, vehicle handling, engine performance or safety systems - the automotive industry is now entering into a new era. Incrementally the car manufacturing sector is becoming a place where electronics in vehicles is becoming more influential, turning cars into connected devices on wheels as technologies are made available – 5G, cloud computing, and more.
A lot of this new functionality centres on autonomous, or self-driving cars, and connected cars, cars which primarily use Internet technology to communicate with external networks, devices and services. The use of particular materials in automotive manufacture are influential in the background.
New Generation Automotive Investment
The predicted investment in this market shows the direction of travel: According to a recent Statista report, the global autonomous car market was valued at over $41 billion in 2024. The market is expected to grow in the following years, reaching a size of nearly $115 billion in 2029. Meanwhile the global connected car market is expected to grow to $191.83 billion by 2028.
As vehicles become more automated and connected, the demand for highly reliable and low-maintenance components is rising. Low friction linings, with their ability to replace traditional bearings, lubricants and coatings, offer a solution that can withstand the rigours of advanced automotive technologies, and not compromise performance.
Fluoropolymer materials, with their outstanding low friction and wear-resistant properties, are paving the way for groundbreaking improvements in vehicle performance and efficiency. Versiv Low Friction Linings (LFL) offer a composite of fluoropolymer, sometimes reinforced with a fibreglass fabric core, that provides such benefits for the evolving sector.
Low Friction Linings: An Essential Contribution
LFL has been instrumental in enhancing the functionality of electromagnetic solenoids used in automatic transmissions, camshaft controls or air suspension systems. These linings significantly reduce friction in moving applications, leading to increased actuation speeds and reduced power requirements. Superior low coefficient of friction not only ensures smooth and consistent movement but also reduces the undesired "slip-stick" effects or hysteresis. This is crucial for automated and connected vehicles, where precision and reliability are essential.
The durability of these low friction materials is another attribute that cannot be overstated. They can operate consistently at temperatures ranging from -180°C to +260°C and their proven longevity, even after wear testing up to 10 million cycles, make them an ideal choice for the demanding environments of practically all private and commercial vehicles. This durability also translates to a lifetime of low maintenance, as these linings replace the need for traditional lubricants that degrade over time or metallic coatings that can be inconsistent in quality.
As well as this, the design flexibility offered by Versiv LFL enables the development of more compact and lightweight components. This not only contributes to overall vehicle efficiency but also offers manufacturers the creative freedom to innovate in design without the constraints imposed by bulkier, less efficient materials.
Dielectric Properties Essential to Success
Fluoropolymer materials unique physical and chemical properties, particularly their excellent dielectric characteristics, make them invaluable in the development of systems essential for the operation of these sophisticated vehicles. In addition to high dielectric strength, the material has low dielectric constant and low dissipation factor.
High dielectric strength refers to the material's ability to withstand electric stress (voltage) without undergoing breakdown. This is crucial in automotive applications where components are often subjected to high voltage but must maintain performance without failure.
A low dielectric constant means that the material can store and release electrical energy efficiently, with minimal energy loss. This property is essential for the accurate and fast transmission of signals, a critical requirement in ADAS systems for rapid information processing.
Low dissipation indicates that the material expresses minimal energy loss in the form of heat when subjected to an alternating electric field. Low energy loss translates to more efficient operation and reduces the risk of overheating in electronic components.
ADAS and radar technologies rely heavily on the efficient, accurate transmission and processing of electromagnetic signals. These systems are designed to detect objects, measure distances, and even identify object types around the vehicle to facilitate actions such as automatic braking, lane keeping, and adaptive cruise control. Fluoropolymer materials, due to their superior dielectric properties, are extensively used in the insulation and encapsulation of electronic components within these systems. They ensure that signal integrity is maintained, preventing interference that could lead to delayed or erroneous signal processing.
Essentially, the automotive industry's shift reinforces the value of Fluoropolymer technology. In a future where vehicles are smarter, more connected, and increasingly autonomous, the demand for components that can reliably perform under varied and demanding conditions will continue to grow in importance.