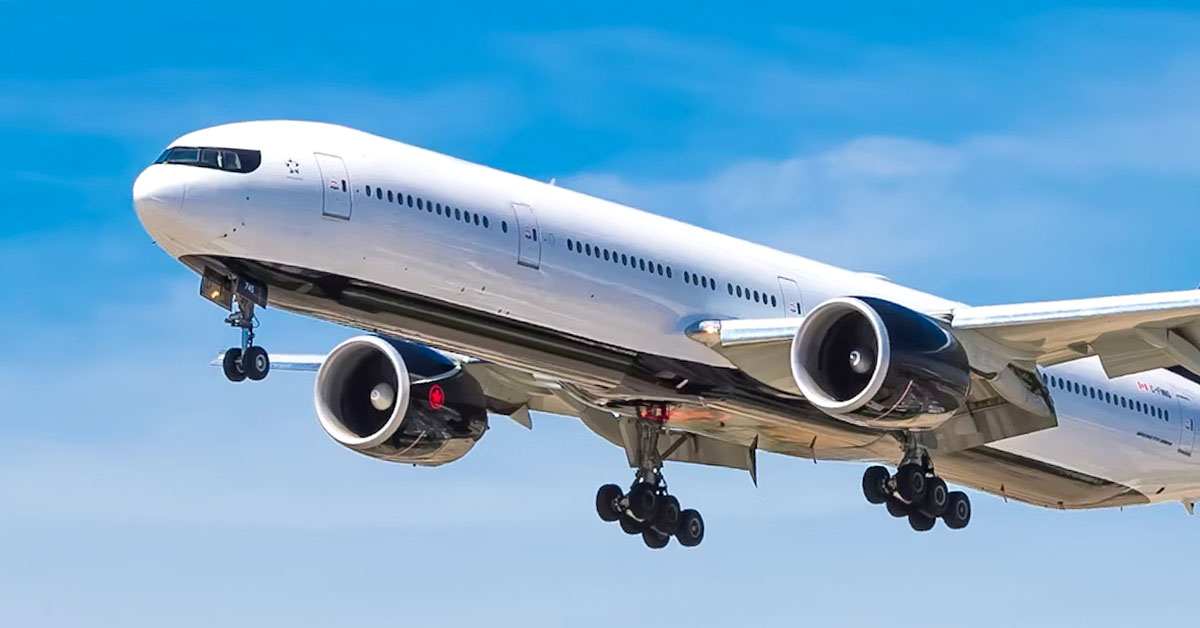
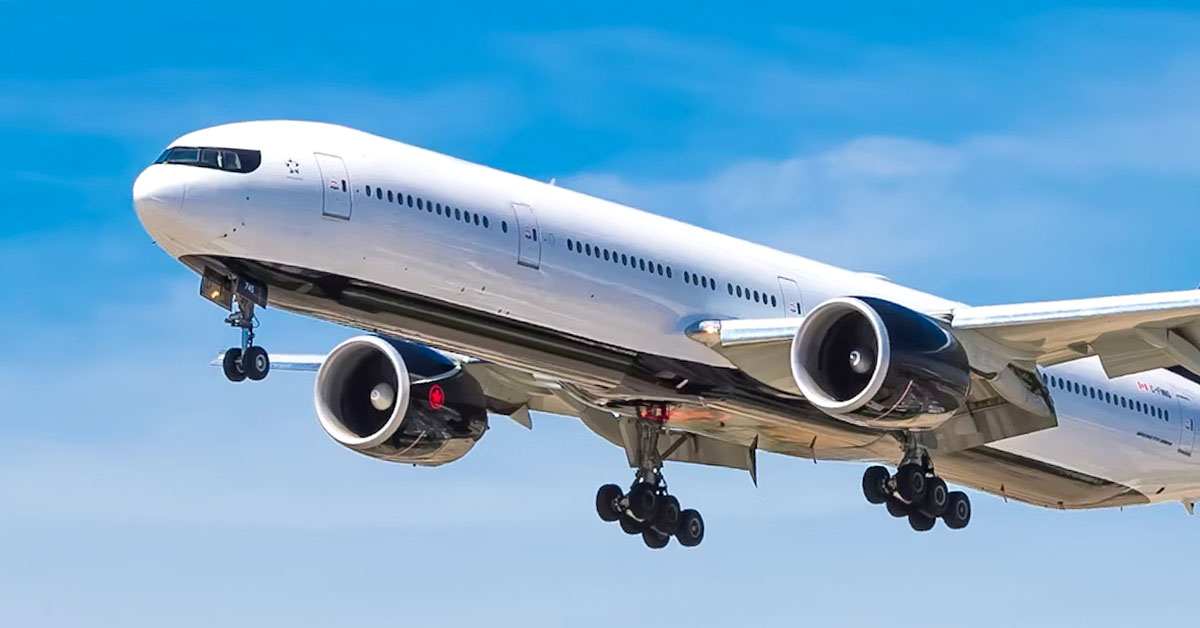
In the aerospace industry, the efficiency and safety of aircraft manufacturing are paramount. The use of PTFE (polytetrafluoroethylene) release solutions, such as Versiv MR1 films, offer numerous advantages over traditional methods.
Key Benefits of PTFE Release Solutions
Essentially, it’s about quality, consistency and making sure to minimise the use of material as much as possible. It is vital to make sure the thinnest possible material gives you good release properties, and good elongation properties so that there is the capability to produce complex shapes. Then there are the fundamentals – temperature resistance and compatibility with whatever resin you use, to ensure processability and freedom of use regarding material combinations.
Colour Differentiation for Process Efficiency
MR1, which meets those requirements, one of our main solutions in this area, is a 1mil film and comes in different colours. This colour differentiation helps manufacturers to distinguish which materials they need to use for steps in the aircraft building process. The MR1 composite material is used as a release film to pack the parts – so in an aircraft application where vacuum bagging consists of multiple layers- with a breather fleece, a release film and a vacuum bag- it gives you the possibility to distinguish for which step of your layering process you must use each material, enhancing workflow efficiency and accuracy.
Ensuring Safety and Compliance in Aerospace Manufacturing
Ultimately the product, which is used by companies such as Boeing and Airbus, is chosen for safety, and our materials are specified. These composite materials must meet stringent standards such as AMS, or AS9100, that ensure safety, performance and reliability across a range of environments. It always has to be the same material so that the quality maintains consistency.
Addressing Modern Manufacturing Challenges
Manufacturers face challenges such as achieving proper release and adapting to increasingly complex part geometries. The MR1 film is engineered to conform to intricate shapes, as seen in modern aircraft designs like the Airbus A350, which features uniquely curved wings. Previously aircraft designs such as the old Airbus A321 were straightforward straight wing creations.
This adaptability for modern aircraft design demands is crucial for maintaining production efficiency.
Additionally, our Versiv CS103S PTFE coated fabric product minimises downtime by allowing for reuse without the need for traditional release agents. This innovation parallels practices in wind blade manufacturing, streamlining processes and reducing waste.
Adapting to Industry Trends for Future Growth
The aerospace landscape is evolving rapidly, with increased competition from manufacturers like Embraer and emerging players in China. As a result, Versiv Composites is committed to adapting to these changes by investing in continuing compliance with industry standards and exploring innovative solutions that meet diverse market requirements.
In conclusion, the integration of advanced PTFE release solutions like Versiv MR1 into lightweight aircraft composite molding not only enhances safety and efficiency but also positions manufacturers to thrive in a competitive market. For more insights into how our products can benefit your operations, visit Versiv Composites.