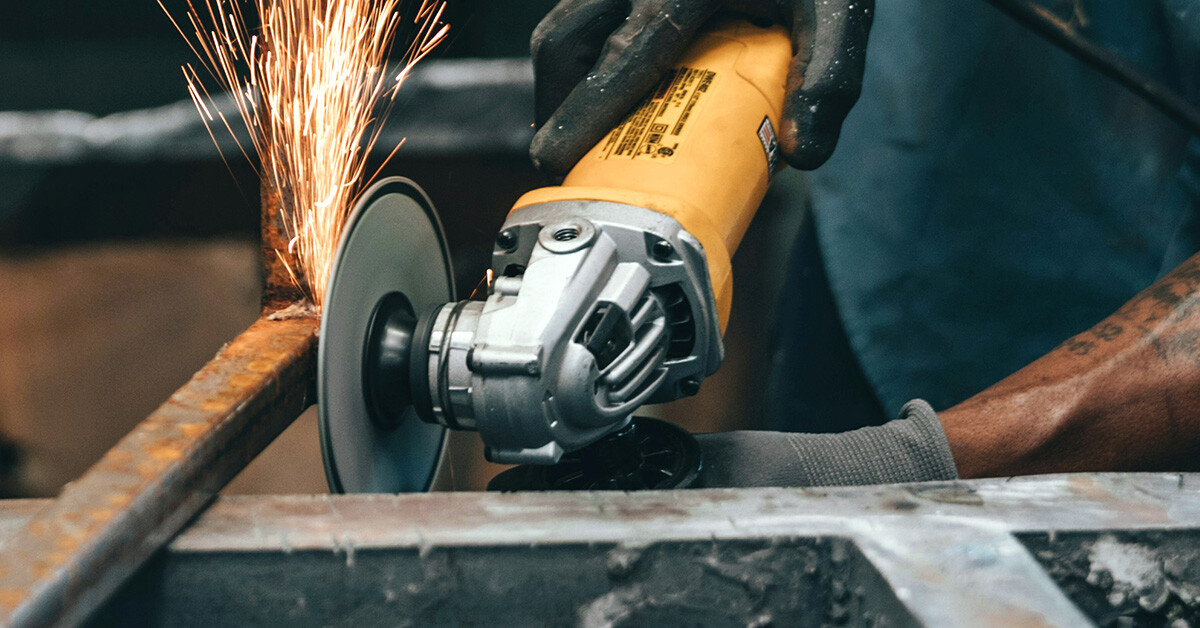
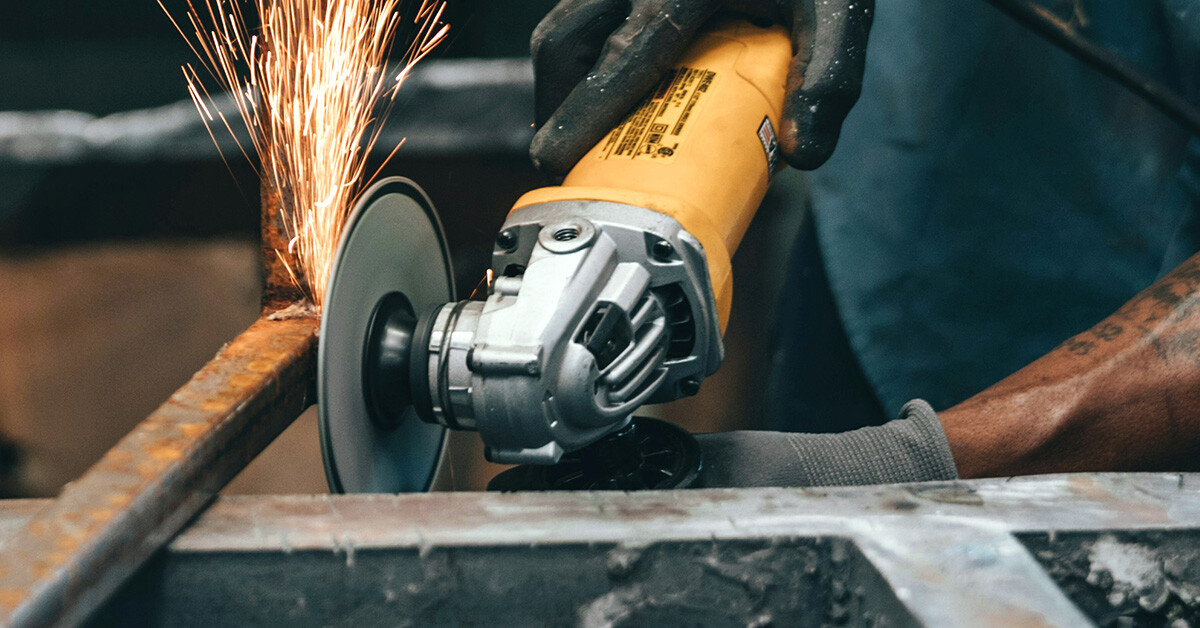
Grinding wheels are used in a diverse range of industries where material removal, surface finishing, and shaping of workpieces are required. Types of grinder wheels are found in metalworking, manufacturing, construction, precision engineering and in medical and dental activities to name but some industrial uses.
Effective grinding wheel performance is essential for achieving efficient material removal, precise surface finishing, and extended tool life in various operations. Grinding wheel release ensures manufacturers can optimise performance, productivity, and cost-effectiveness, leading to improved efficiency and higher-quality finished products.
Role of PTFE coated fabric in grinding wheel release in industry
PTFE coated fabrics high-temperature release capability means the release material remains stable in temperatures where PVC on grinding discs are cured.
After the log is cured in a high-temperature oven, the individual grinding wheels can be separated from each other through PTFE fabric separator sheets sited in between. The combination of clean release properties offered by PTFE coating and strength of fiberglass substrate allows for clean, reliable separation. The diameters of the die cut separator sheets vary, depending on the size of the end product, as specified by the customer.
Surface texture is an important variable and material selection depends on the desired release characteristics. This could include whether the end product requires an embossed pattern or surface texture, for example, which can be created by the texture of the separator fabric.
Materials can be provided according to whether high end or lesser quality discs are required. Surface roughness is critical to the texture of the grinding wheel disc, with specific roughness applied to each role. If this feature is not accurate, the material will prematurely fail. In addition, weight is critical to roughness – the more PTFE applied, the smoother the release.
Key properties of PTFE-coated fabrics that ensure reduced waste and higher efficiency
Versiv Composites can customise release material to adapt to various demands in the high temperature curing process of grinding wheel and abrasive discs, eliminating the need to regularly clean press plates.
The grinding wheel is subjected to elevated temperatures to facilitate the cross-linking and hardening of bonding agents and PTFE fabrics can withstand these high temperatures without melting or sticking to the grinding wheel, providing a reliable and durable surface for the curing process.
PTFE's non-stick properties prevent the grinding wheel from sticking to the fabric during the process, enabling easy and clean removal once the curing is complete. This helps in preventing damage or deformities to the grinding wheel.
Interested in purchasing coated fabrics for more effective grinding wheel performance?
To summarise, the properties inherent to PTFE contribute to a smoother and more efficient curing process, leading to high-quality grinding wheels with minimal defects or damage. Contact our team at Versiv today to learn more about how these products can benefit your project.