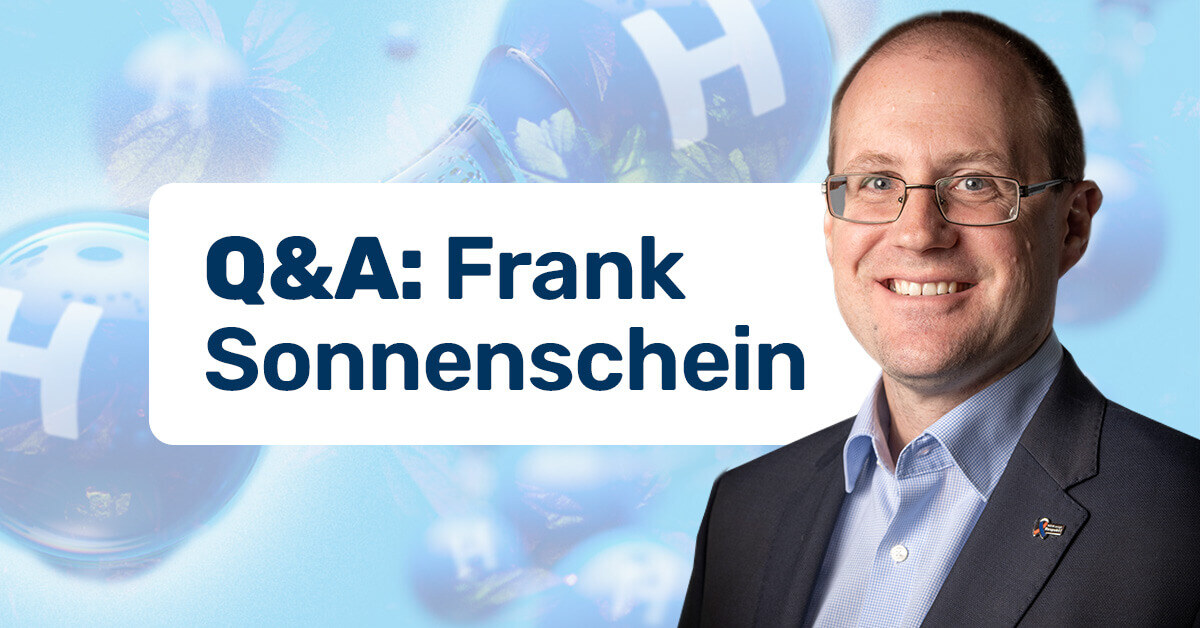
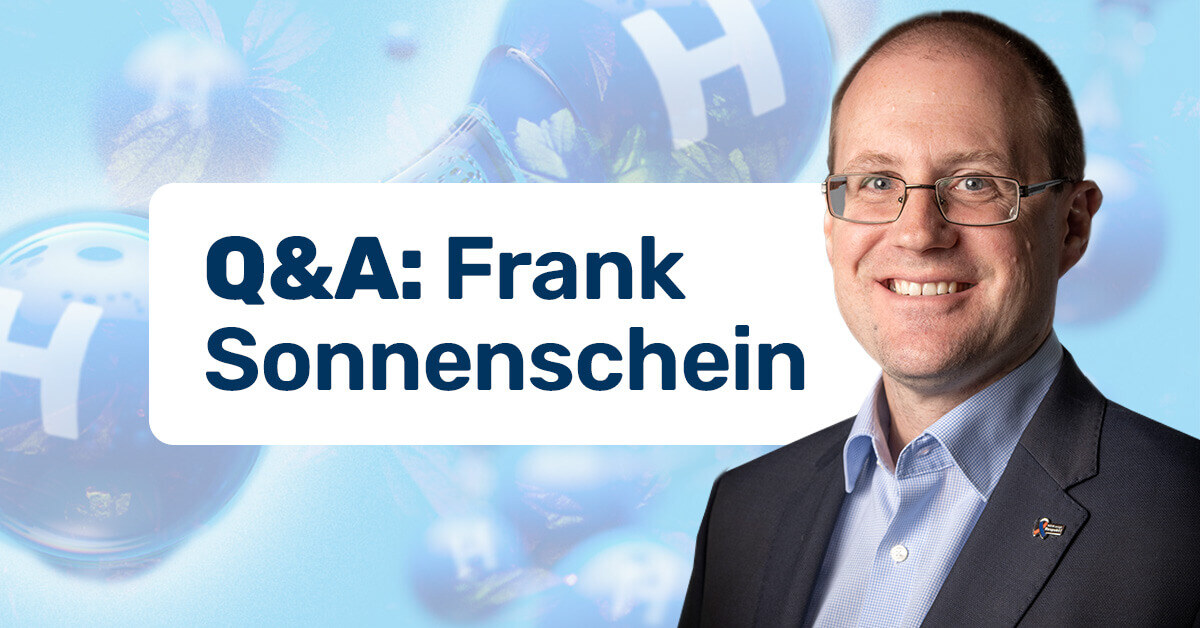
Tackling the challenges of hydrogen with new advanced sealing technologies
Hydrogen technologies stand at the forefront in the quest for a sustainable future, offering clean energy solutions to a wide range of industries and applications. Securing the durability and efficiency of these technologies, however, may pose significant challenges.
This week we asked Frank Sonnenschein, Global Business Development Manager for Hydrogen, about the new developments in sealing materials that support fuel cell and electrolyser technologies in tackling with media, thermal and mechanical conditions.
Q: How do sealing materials enhance performance in fuel cells and electrolysers under varied operational conditions?
A: Advanced sealing materials are engineered to meet the demanding requirements of both polymer exchange membrane fuel cells (PEMFC) and electrolysers (PEMEL), ensuring integrity despite dynamic fluctuations. These sealing materials adeptly manage shifts in temperature from -30°C to 180°C and pressures beyond 3 bars.
In general, there are two different material-groups in use. Elastomers and plastics (mainly PTFE based). Both PTFE and elastomers have limits. Elastomers are a good sealing material with good decompression, but it has limited media and temperature resistance. PTFE, diametrically, has limited seal-ability but is very good in temperature and media resistance. The ideal is to co-develop with clients to merge the resilience of elastomers with the robustness of PTFE, offering solutions that excel in high-temperature and media resistance, which is crucial for hydrogen technology applications.
Q: What advancements in thermal hysteresis resistance have been developed to boost the longevity and reliability of stacks in fuel cells and electrolysers?
A: Tackling the issue of thermal cycling, especially in automotive fuel cells, Versiv has innovated materials that demonstrate superior mechanical stability. By employing glass fabric or polyimide reinforced composite materials effectively, such as the introduction of DF2929, PTFE coated polyimide, these materials counteract the thermal hysteresis effects seen with frequent starts and stops. This innovation aims to continually improve the durability and reliability of fuel cells and electrolysers, pivotal components of hydrogen technology.
It is important for us to understand what the customer faces in terms of media and temperature range to co-develop the optimal solution.
Q: How does strict control over the thickness tolerance of sealing materials contribute to increased efficiency and power density in hydrogen technologies?
A: Sealing materials, maintaining a tight thickness tolerance, play a critical role in optimising the performance and efficiency of fuel cells and electrolysers. The tighter our thickness tolerance is, the better the pressure distribution coming from the screws can be calculated and achieved, leading to less force needed or/and gas-tighter systems.
This precision directly impacts the operational integrity of the Gas Diffusion Layer (GDL), preventing its over compression, which can detract from overall system efficiency. While the effect on electrolyser efficiency enhancement might be considered indirect, the contribution of these sealing materials to the streamlined assembly and reliable performance of fuel cells underscores their value in hydrogen technology.
Q: Can you elaborate on the material properties that enable Versiv products to maintain operational integrity under the diverse conditions fuel cells and electrolysers encounter?
A: Key to product efficacy in hydrogen technology is the emphasis on temperature stability and media resistance, supplemented by mechanical durability. These sealing materials are designed to withstand increases in operational demands, such as pressure shifts from 2 to 3 bars, without compromise. Defined surface finish and stringent control over thickness tolerance further enable their suitability for differing electrochemical technologies, ensuring Versiv Composites solutions meet the rigorous demands of fuel cells and electrolysers alike.
Q: How do sealing solutions mitigate the challenges posed by varied chemical environments in hydrogen and oxygen chambers of fuel cells and electrolysers?
A: Leveraging the inherent inertness of PTFE, Versiv sealing solutions are adept at navigating the diverse chemical landscapes within hydrogen technologies.
Whether facing hydrogen exposure on the anode side or the humidified air/liquid water on the cathode side of fuel cells, PTFE-based sealing materials remain impervious to most media, ensuring compatibility and performance across a broad pH spectrum. This capability is critical for the effective separation of hydrogen and oxygen chambers in fuel cells and electrolysers, reinforcing the role of Versiv materials in advancing hydrogen renewable energy technology.