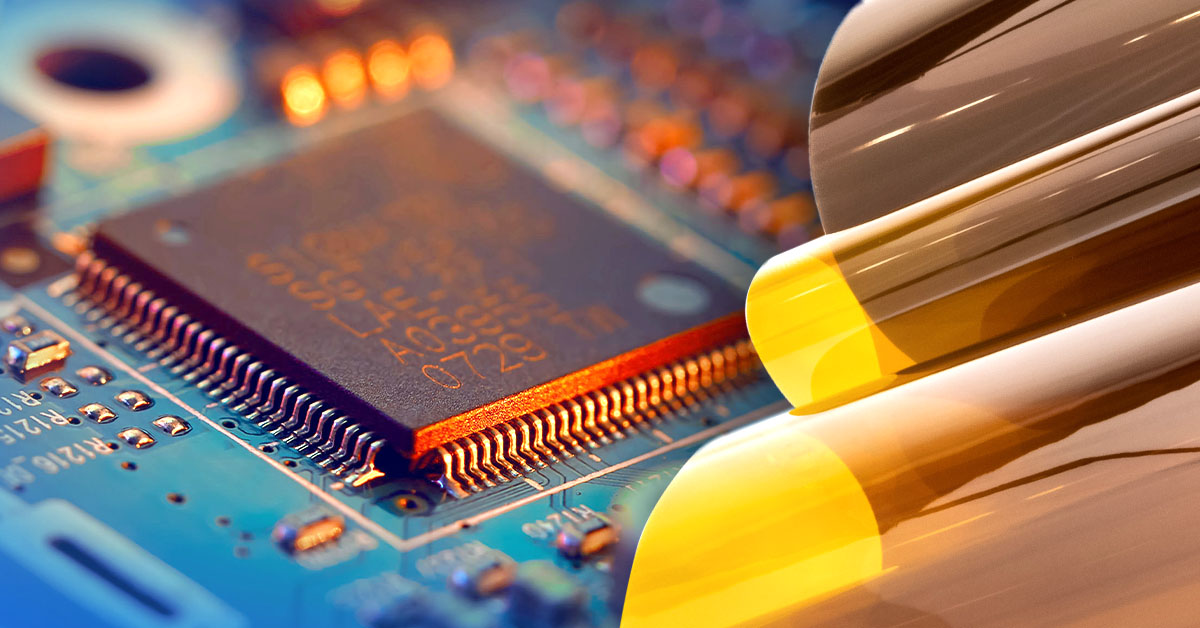
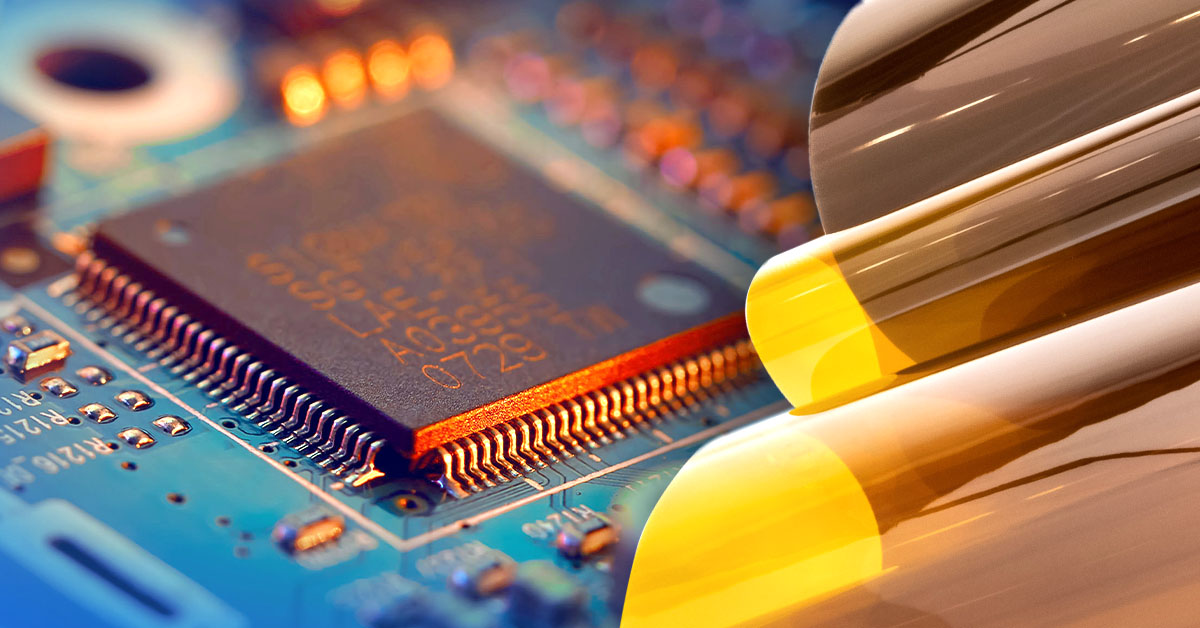
The rapid evolution of communication technologies — driven by advancements like 5G infrastructure or Artificial Intelligence — requires materials capable of meeting increasingly stringent performance demands.
By addressing challenges related to signal integrity, manufacturing efficiency, and miniaturisation, PTFE composites are positively influencing the future of electronic systems. These materials are also emerging as potential solutions for the fabrication of copper clad laminates (CCLs), which are substrates present in high-frequency and high-density printed circuit boards (PCBs).
Enhancing Signal Integrity at High Frequencies
Signal integrity is essential in modern communication systems operating at GHz frequencies. PTFE-based materials excel in this domain due to their unique dielectric properties:
- Low Dielectric Constant (Dk): A lower Dk minimises signal propagation delays and reduces impedance mismatches—key factors in maintaining signal quality.
- Low Dissipation Factor (Df): With Df values as low as ~0.0002 at high frequencies, PTFE ensures minimal dielectric loss during signal transmission.
- Thermal Stability: Stable dielectric performance across wide temperature ranges prevents phase distortion caused by thermal fluctuations.
- Resistance: Hydrophobic PTFE resists water ingress that would otherwise degrade dielectric properties.
These attributes make PTFE composites indispensable for RF systems, microwave devices, and advanced digital communication networks.
Advanced Electronic Materials and Manufacturing Efficiency
The production of copper clad laminates demands precision and consistency — qualities that PTFE-materials deliver through innovative processes:
- Minimised Defects: Versiv cast film process eliminates voids where conductive anodic filaments could form, reducing the possibility of spot defects and improving yield rates.
- Dimensional Stability: Silica fillers enhance dimensional stability during multi-layer laminate production, ensuring precise tolerances even under demanding conditions.
By streamlining manufacturing processes and reducing defect rates, these composites enable manufacturers to achieve higher efficiency and reliability.
Enabling Miniaturisation Without Compromising Performance
As electronic components become thinner and lighter, material innovation becomes critical. Advanced composite films address these challenges by offering:
- Thinner layers compared to traditional fabric-based solutions.
- Stronger dielectric performance
- Increased homogeneity
These features not only support miniaturisation but also reduce mechanical stress on equipment—allowing faster cycle times and easier handling during production.
Supporting 5G Infrastructure and High-Bandwidth Applications
The transition to 5G networks demands materials capable of supporting higher data rates with minimal signal loss. Versiv patented filler loading distribution enables modulation of dielectric constant (Dk) while maintaining low dissipation factor (Df) and thermal expansion coefficients (CTE).
Unlocking Competitive Advantages Through Customisation
Customisation is a cornerstone of modern material innovation. Versiv empowers electronics manufacturers with flexibility in thickness adjustments, tailored Dk values, and optional bonding layers—allowing the company to develop proprietary solutions that differentiate their products in specialised markets.
Conclusion
PTFE composite materials are not just enhancing today’s communication systems — they are set to facilitate tomorrow’s technological breakthroughs. By combining superior dielectric performance with manufacturing efficiency and adaptability, these materials are driving progress across industries reliant on high-frequency communication systems. As we move toward a more connected world powered by 5G networks and beyond, advanced PTFE composites will remain influential.