Non-stick release LVT belt solutions
In today’s flooring market, Luxury Vinyl Tiles (LVT) are an increasingly popular cost-effective solution for commercial and residential buildings. The broad range of LVT finishes — which can resemble wood, tile and slate — means manufacturers must be adept at meeting the growing demand for various customer tastes.
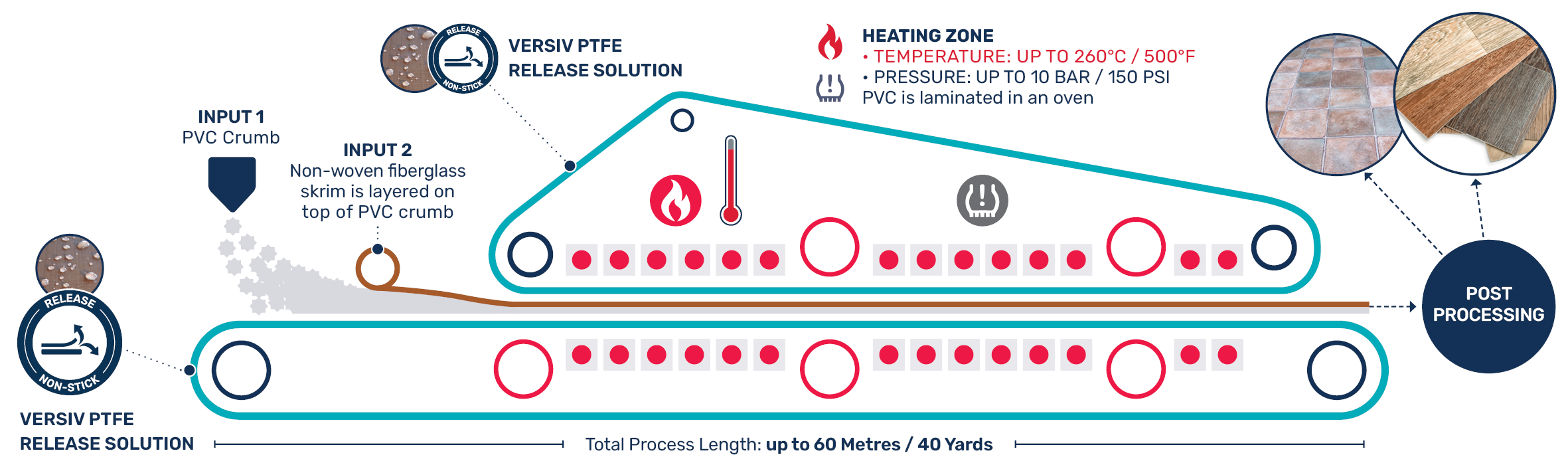
Versiv PTFE release solutions enable roll-to-roll processing of LVT manufacturing due to its ability to withstand high pressure (up to 10 Bar / 150 PSI) and elevated temperatures (up to 260°C / 500°F) conditions associated with the lamination process.
Mechanically durable, with consistent “easy release” properties, the Versiv process conveyor belts provide longevity, high production efficiency, and a reduction in manufacturing downtime. They also eliminate the need for silicone sprays and release agents, which are costly and time-consuming.
Versiv PTFE belts can be configured for every type of machine and are available with 2 ply options, such as an anti-static machine-facing ply and/or textured surface to assist in off-gassing during lamination. They feature a low-profile seam that does not increase thickness and enables no “mark-off” or imprint at the joint.