Essential Protection during PCB Coverlay
In today’s electronics market, the requirement for thinner, lighter, faster and more power-efficient electronics is impacting all industries. Flexible printed circuit boards (FPCB) are a leading core component choice because of their design flexibility and size.
Building FPCB is a complex multi-step process. Each critical step carries a risk of defect. The coverlay lamination process fully encapsulates the delicate structure of FPCB, giving protection and insulation.
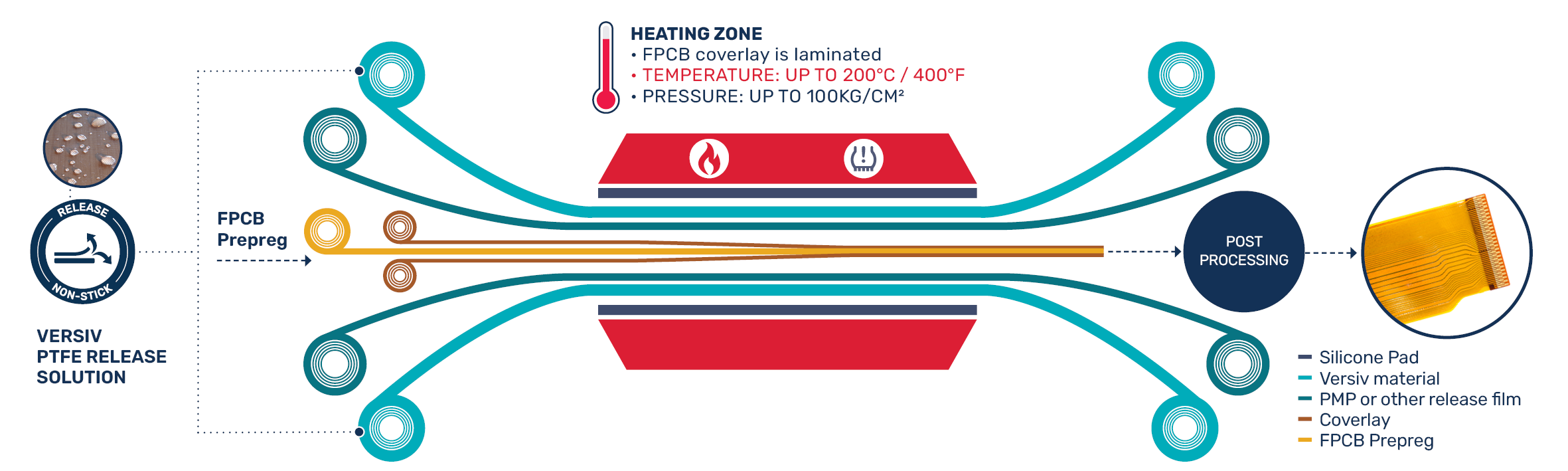
Versiv high-performance PTFE-coated fabrics provide essential protection for the very delicate FPCB. During lamination, the protective outer layers of polyimide and other coverlay films are bonded onto one or both sides of the fragile FPCB at high temperatures of up to 260°C / 500°F.
The dimensionally stable and robust Versiv rolls are tensioned, enabling the “throwaway” single-use PMP or other release films to be easily pulled into the laminator, reducing the risk of creasing, which can result in defective FPCBs. In this aggressive and sticky lamination process, molten adhesives, high temperature and pressure can cause the release of contaminants. The PMP or other release films supported by the Versiv PTFE coated fabrics provide an effective barrier layer by blocking grease and oils from the silicone cushioning pads.
Defect rate improvements are made possible with Versiv release solutions due to their spot-free surface. This super smooth, nonstick and defect-free PTFE surface prevents the build-up of any hard sticking points from molten polymers, which can frequently occur after long-term repetitive cycles. Versiv release solutions after repetitive use continues to offer excellent and consistent release.
Consistent mechanical and surface release properties over time are the key to a longer lifetime. The high mechanical strength and good wear-resistant PTFE-coatings of Versiv release belts enable long lifetimes and multiple usages. This means continuous production with consistent batch-to-batch quality, reducing machine downtime and maximising the cost/performance ratio.