Versiv Manufacturing Aids: PTFE Sheet and Belt
Compression molding is the most cost-effective option for the production of a range of lightweight, high strength interior automotive parts.
Versiv release solutions for compression moulding are used as processing aids when converting, bonding and shaping materials into composite parts. They are compatible with many press forming processes where they protect the reusable molds from the molten substrates and ensure easy release. Excellent temperature, mechanical strength and abrasion resistance allows precise reproducibility and reduces overall cost.
Versiv non-stick release sheets and belts can be configured for every type of machine with features such as guidable edges, different types of joints, and higher strength and textured options.
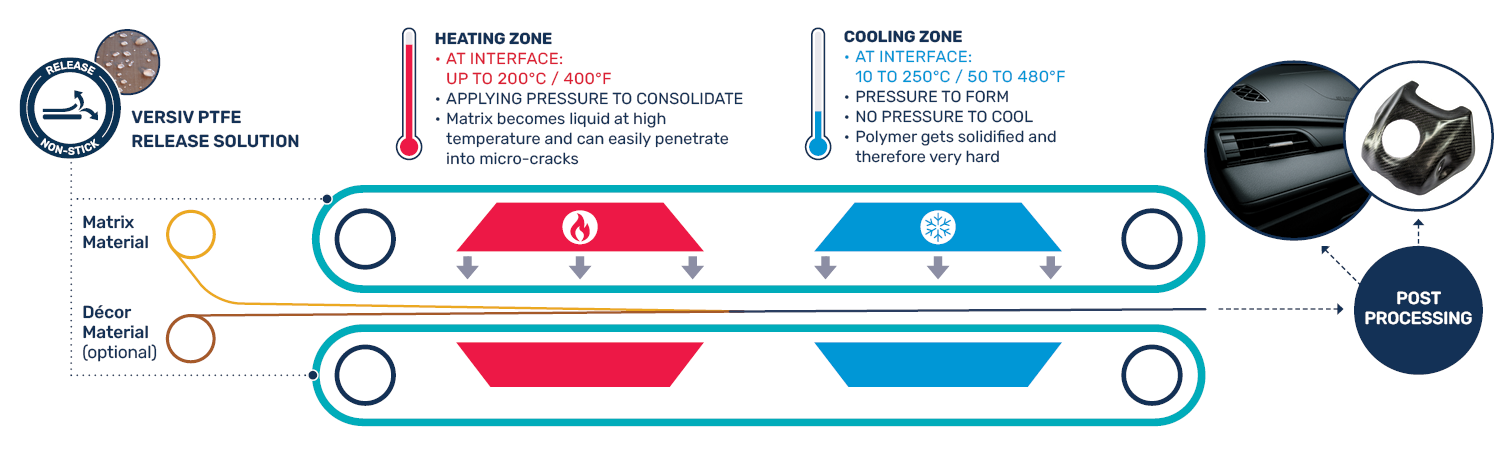
Versiv process conveyor belts transport the mixture through the oven to the molding process where pressure and heat are applied to the resins and reinforcement materials where they are bonded to form a composite material for further processing. The conditions of curing must be carefully selected and closely monitored to make certain the product attains the desired geometry and shape.
Versiv very smooth and non-stick release surface allows for the composite to solidify and be released from the mold in a continuous operation. The easy and consistent PTFE mold release allows for quick mold clean-up. It also eliminates the need for using release agents or silicone sprays, reducing the time between cycles.